Haber-Bosch prosess
Den Haber-Bosch-prosessen er en stor-skala industriell kjemisk prosess for syntese av ammoniakk . Den er oppkalt etter de tyske kjemikerne Fritz Haber og Carl Bosch som utviklet prosessen på begynnelsen av 1900-tallet. Det sentrale trinnet i prosessen, ammoniakk-syntesen fra atmosfærisk nitrogen og hydrogen , utføres på en jernholdig katalysator ved trykkfra 150 til 350 bar og temperaturer fra omtrent 400 til 500 ° C utført. Som en viktig kjemisk prosess med en produksjon på mer enn 150 millioner tonn i 2017, dekker den mer enn 99% av den globale ammoniakkproduksjonen.
Ammoniakk er et kjemisk stoff som hovedsakelig brukes til produksjon av urea , ammoniumnitrat , ammoniumsulfat og ammoniumfosfater . Disse stoffene brukes som gjødsel og bidrar til ernæring til en stor del av verdens befolkning. Ammoniakk brukes også til produksjon av eksplosiver og andre nitrogenholdige kjemikalier. Den selektive katalytiske reduksjonen ved bruk av ammoniakk i røykgassdenitrifiseringen for omdannelse av skadelige nitrogenoksider til nitrogen og vann. Ammoniakk har også blitt brukt som et miljøvennlig og energieffektivt kjølemedium siden 1876 .
De vitenskapelige prestasjonene for realiseringen av denne prosessen var på den ene siden undersøkelsen av den underliggende kjemiske reaksjonen av Fritz Haber og Walther Nernst , på den andre siden det systematiske søket etter passende katalysatorer av Alwin Mittasch , samt avklaring av grunnleggende prosessteknikk. problemer for høytrykksprosesser av Carl Bosch. I forbindelse med Haber-Bosch-prosessen tildelte Nobelstiftelsen Nobelprisen for kjemi til Fritz Haber i 1918 , til Carl Bosch i 1931 og til Gerhard Ertl i 2007 , som fant den fullstendige teoretiske forklaringen på mekanismen for ammoniakkdannelse.
historie
Brød laget av luft
Fra arbeidet til Justus von Liebig har det vært kjent siden midten av 1800-tallet at opptaket av nitrogenforbindelser er et grunnlag for vekst av avlinger. De nødvendige nitrogenforbindelsene ble tilført jordbruket via gjødsel, kompost eller gjennom en spesifikk vekstrotasjon . På grunn av den raske veksten av verdensbefolkningen på 1800-tallet, kunne den tilhørende høye etterspørselen etter nitrogengjødsel ikke lenger imøtekommes av naturlige forekomster av guano eller Chiles nitrat, for eksempel, eller av tekniske kilder som koksovnsgass . For å gjøre oppmerksom på dette faktum holdt den britiske kjemikeren William Crookes en anerkjent tale til British Association for the Advancement of Science i Bristol i juni 1898 . I den uttalte han at etter 1918 ville etterspørselen etter nitrogenforbindelser langt overstige tilbudet, og at den vestlige verden ble truet med en hungersnød av ufattelig proporsjoner. Han fortsatte med å si at den eneste løsningen på dette problemet var å kjemisk fikse nitrogenet i luften. Han kalte den tekniske gjennomføringen av denne prosessen en av de store utfordringene for kjemikerne i sin tid. Forsøket på å binde nitrogen i atmosfæren i et kjemikalie som planter kan absorbere, kjent under slagordet "Brød fra luft", gikk deretter videre til å bli et av fokuspunktene for kjemisk forskning på den tiden.
Tidlig utvikling

Et første gjennombrudd i fiksering av atmosfærisk nitrogen kom i 1898 med fremstilling av kalsiumcyanamid i henhold til Frank Caro-prosessen , der kalsiumkarbid absorberer atmosfærisk nitrogen ved høye temperaturer og dermed fikser det. Den hydrolyse av kalsiumcyanamid gir ammoniakk og kalsiumkarbonat . Selv om det ble bygget opp store kapasiteter for produksjon av kalsiumcyanamid, var prosessen ikke konkurransedyktig på lang sikt på grunn av det høye energibehovet på rundt 190 gigajoules per tonn ammoniakk.
I 1900 registrerte Wilhelm Ostwald patent på "produksjon av ammoniakk og ammoniakkforbindelser fra gratis nitrogen og hydrogen" fordi han tilsynelatende hadde lykkes med å produsere ammoniakk katalytisk fra grunnstoffene. Allerede i 1903 publiserte Rottweiler-eksplosivprodusenten Max Duttenhofer Ostwalds advarsel om en saltpeterembargo i tilfelle krig i "Schwabisk Merkur". Ostwald trakk patentet sitt etter at Bosch hadde bevist at den produserte ammoniakken kom fra jernnitridet til den katalysatoren som ble brukt.
Den Birkeland-Eyde-prosessen , som er utviklet av Norsk vitenskaps Kristian Birkeland og hans forretningspartner Sam Eyde og satt i drift i 1903, fiksert nitrogenet i luften ved å oksydere det direkte til nitric oxide ved hjelp av en elektrisk lysbue . Ved avkjøling og ytterligere oksidasjon ble lystgass dannet , som reagerte på salpetersyre ved absorpsjon i vann. Den lave energieffektiviteten førte snart til at prosessen ble fortrengt.
Grunnleggende arbeid
I 1904 begynte Fritz Haber, som på den tiden jobbet som førsteamanuensis for teknisk kjemi i Karlsruhe , å håndtere de kjemiske fundamentene i ammoniakk-syntese. Likevektskonstanten som ble funnet for syntesen av ammoniakk fra elementene nitrogen og hydrogen tilsvarte et utbytte på mindre enn 0,01 prosent ved en temperatur på 1000 ° C og normalt trykk og var derfor for lavt til å gjennomføre en teknisk prosess. Haber var klar over at høyere trykk ville føre til bedre avkastning, men på grunn av de forventede tekniske problemene stoppet han midlertidig forskningen på dette området. Bare en vitenskapelig diskusjon med Walther Nernst om likevektskonstanten i ammoniakk-syntese basert på Nernst-teoremet fikk Haber til å fortsette sitt arbeid. Som et resultat av videre forskning anså han overføringen til teknologi bare mulig ved temperaturer under 300 ° C og bare med en passende katalysator . Rett etterpå var han i stand til å praktisere det ved hjelp av en osmiumbasert katalysator.
13. oktober 1908 søkte Haber til det keiserlige patentkontoret i Berlin om patentbeskyttelse for en "metode for syntetisk fremstilling av ammoniakk fra elementene", som den innvilget 8. juni 1911 med patentnummer 235.421. Siden han nå jobbet med BASF , ga han selskapet patentet for kommersiell bruk.
teknisk realisering
Spesielt tilførselen av råstoffet hydrogen, som til da bare var tilgjengelig i større mengder i klor-alkali-elektrolyse , krevde helt nye prosesser. Også for konstruksjonen av de kjemiske reaktorene som er nødvendige for ammoniakk- syntese , der hydrogen kan kontrolleres ved høyt trykk og temperaturer, var det ingen referanser i teknologien før da. Carl Bosch og Fritz Haber utviklet deretter nye løsninger innen mange områder innen teknisk kjemi og reaktorkonstruksjon.
På grunn av det store antallet spesialister som kreves for å implementere produksjon i industriell skala, grunnla Bosch en tverrfaglig kjemisk ingeniøravdeling der mekaniske ingeniører og kjemikere jobbet sammen. Siden stålene opprinnelig ble brukt for reaktorkonstruksjon erodert av atomisk diffust hydrogen, var en av oppgavene til det nye arbeidsområdet å undersøke materiell skade forårsaket av avkalking av karbonstål . Dette førte til slutt til utvikling av høylegerte krom-nikkelstål som tåler hydrogenangrep ved de nødvendige reaksjonstemperaturer og trykk. Spesielt Schierenbeck-viklingsprosessen utviklet av Julius Schierenbeck , der flere lag varmt metallbånd ble krympet på et kjemisk motstandsdyktig sentrerør, gjorde det mulig å bygge større og sikrere høytrykksreaktorer. Samtidig utviklet og testet Alwin Mittasch rundt 3000 forskjellige katalysatorer basert på jernoksid med forskjellige konverteringsakselererende stoffer, som han kalte aktivatorer eller promotorer , i 20 000 eksperimenter . Katalysatoren som ble brukt i 2015 tilsvarte i stor grad den som ble utviklet av Mittasch.
I 1913 bestilte BASF for første gang et anlegg basert på Haber-Bosch-prosessen ved Ludwigshafen-Oppau- anlegget . Anleggets kapasitet var i utgangspunktet 30 tonn per dag. Allerede i 1914 presset den tyske stabssjefen Erich von Falkenhayn den videre utviklingen av prosessen til den industrielle anvendeligheten , hvorpå Bosch ga det såkalte saltpeterløftet . Dette var en kontrakt for levering av nitrater med kjøpsgarantier og med økonomisk støtte fra Reich for bygging av tilsvarende anlegg. Dette skal gjøre det mulig å produsere ammoniumnitrat som grunnlag for militære eksplosiver i tilstrekkelige mengder uten den naturlig forekommende salpeteren som ellers brukes. Rett etterpå lyktes Haber-Bosch-prosessen i å produsere tilsvarende store mengder av krigsmaterialet. Dette gjorde det tyske imperiet, avskåret fra nitrogenkilder som Chiles nitrat av den britiske marineblokaden, i stand til å opprettholde ammunisjon og gjødselproduksjon under første verdenskrig og forhindre økonomisk kollaps. I tillegg til det store anlegget i Oppau nær Ludwigshafen , ble andre i Leuna og Bitterfeld drevet av BASF og, etter fusjonen i det store tyske selskapet, av IG Farben .
Etter første verdenskrig
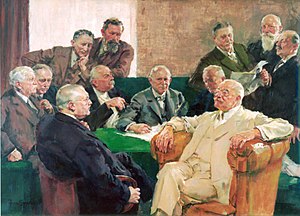
Etter krigen forpliktet den seirende makten Frankrike BASF ved en avtale om å overgi alle patenter og erfaringer fra prosessen og støtte byggingen av en tilsvarende fabrikk i Toulouse . Ytterligere ammoniakkanlegg ble bygget i England, Italia og andre land samtidig. Dette byggeprosjektet var basert enten på en lisens fra BASF eller på en prosessvariant med modifiserte prosessparametere, inkludert Casale-prosessen og Mont-Cenis-prosessen med modifisert katalysator.
IG Farben ble grunnlagt i perioden mellom de to verdenskrigene, med Carl Bosch som sin første konsernsjef. Allerede i 1926 var selskapets markedsverdi , som nå har 100 000 ansatte, rundt 1,4 milliarder riksmarker . Den globale økonomiske krisen som begynte med aksjemarkedskrasj i New York i oktober 1929, reduserte etterspørselen etter syntetisk ammoniakk betydelig. Produksjonen i Tyskland, som allerede hadde nådd et årlig volum på over 800.000 tonn, falt da til under 500.000 tonn og IG Farbens inntekt ble halvert. Likevel forble IG Farben verdens største produsent av ammoniakk frem til 1930; Ammoniakk-syntese utgjorde 65 prosent av det totale overskuddet.
Importembargo for nitrogengjødsel utstedt av Brüning-skapet gjorde det mulig for IG Farben å heve prisene på syntetisk gjødsel igjen. Etter maktovertakelsen av Hitler overtok naziregimet kontrollen over IG Farben. Som svar på presset fra naziregimet trakk Bosch seg sin stilling i styret i 1935, som falt til NSDAP- medlem og militærøkonomisk leder Hermann Schmitz . I 1940 nådde ammoniakkproduksjonen i Tyskland en million tonn per år. Som et resultat av den stadig økende etterspørselen etter ammoniakk og dets sekundære produkter ble det opprettet stadig kraftigere reaktorer.
Etter andre verdenskrig
Den økende tilgjengeligheten av billig råolje og kostnadsreduserende forgassingsprosesser gjennom for eksempel delvis oksidasjon av råoljefraksjoner gjorde det mulig å sette opp Haber-Bosch-fabrikker over hele verden etter andre verdenskrig. Den delvise oksydasjonen som opprinnelig ble utviklet av IG Farben ble forbedret av selskapet Imperial Chemical Industries (ICI) og utvidet til å omfatte oksidasjon av nafta , noe som gjorde råvarene til prosessen billigere på 1950- og 1960-tallet.
Ingeniørfirmaer som MW Kellogg utviklet senere mer energieffektive og derfor mer kostnadseffektive store anlegg med bare en reaktor, noe som førte til en verdensomspennende økning i anleggskapasiteten . Økende konkurranse og høyt kostnadstrykk banet endelig vei for LCA-prosessen fra ICI og KAAP-prosessen fra Kellogg, Brown & Root , der en ruthenium-katalysator ble brukt for første gang .
råvarer
Ammoniakk opprettes i en likevektsreaksjon fra grunnstoffene hydrogen og nitrogen i henhold til ligningen
- ,
hvorved det nødvendige nitrogenet tas fra den omgivende luften. Oksygenet, som også er inneholdt i luften, men som er uønsket, ble først omdannet til vann ved reduksjon med hydrogen og således separert; Fauser-prosessen brukte nitrogenet, som ikke ble omdannet under ammoniakkforbrenning med luft, som råmateriale. Senere viste nitrogenproduksjonen ved luftseparasjon i henhold til Linde-prosessen å være mer økonomisk.
Den største delen av produksjonskostnadene er anskaffet av hydrogen, som opprinnelig ble hentet fra kostnadskrevende klor-alkali-elektrolyse . Med naturgass, råolje, kull og elektrolyseprodukter av vann ble andre kilder for produksjon av hydrogen tilsatt senere.
BASF brukte vanngass basert på kullgassifisering av brunkull ved hjelp av en Winkler-generator som den primære kilden. Hydrogenet oppnås ved å reagere damp med glødende koks. Luften som tilføres doseres på en slik måte at oksygenet blir fullstendig omdannet til karbonmonoksid . Nitrogenet som kreves for den påfølgende ammoniakk-syntesen ble værende i vanngassen. Karbonmonoksydet ble deretter omdannet til lett fjernbar karbondioksid eller brukt i en vann-gass skiftreaksjon for å gi ytterligere hydrogen. I 2008 ble omtrent 18 prosent av hydrogenet produsert over hele verden produsert av kull som råvare.
Selv om naturgass ennå ikke var tilgjengelig for BASF som råmateriale for produksjon av hydrogen på 1920-tallet, startet Carl Bosch allerede utviklingen av dampreformeringen av metan , som senere skulle bli en viktig del av prosessen. Georg Schiller oppnådde et gjennombrudd for IG Farben, som lyktes i å dampreformere metan ved hjelp av en nikkeloksydkatalysator. Den Standard Oil of New Jersey ble gitt konsesjon til hydrogenproduksjon ved dampreformering ved anlegget i 1931 Baton Rouge i Louisiana begynte. Dampreformeringen av naturgass utgjorde rundt 48 prosent av den globale hydrogenproduksjonen i 2014, hvorav rundt 60 prosent brukte Haber-Bosch-prosessen.
En annen mulig metode for å produsere hydrogen er delvis oksidasjon . I dette tilfellet er naturgass eller petroleumsopprinnelse hydrokarboner forgasset med oksygen og damp i en åpen reaktor uten en katalysator ved ca. 1100 ° C, og syntesegassen viderebehandlet som i dampreformeringen. De høyere hydrokarboner fra petroleum bidro med 30 prosent til den årlige produksjonen av hydrogen i 2008.
Hydrogen kan også oppnås ved elektrolyse av vann. Dette bruker elektrisk energi til å bryte ned vann til hydrogen (H 2 ) og oksygen (O 2 ). Denne prosessen er bare økonomisk hvis billig elektrisk energi, for eksempel fra vannkraft, er tilgjengelig. I 2008 utgjorde elektrolyse rundt fire prosent av hydrogenproduksjonen.
Med fremveksten av plattformkapasitet i USA på midten av 1950-tallet, ble en petrokjemisk hydrogenkilde tilgjengelig som i 1956 ga omtrent elleve prosent av hydrogenet som kreves for ammoniakk-syntese i USA. Andre raffineri-prosesser som hydroavsvovling og hydrokraking brukte senere det produserte hydrogenet.
katalysator
For å senke aktiveringsenergien og den tilhørende økningen i reaksjonshastigheten , brukes et ekstra stoff, katalysatoren , i mange kjemiske prosesser , som ikke forbrukes under reaksjonen. Hvis den fysiske tilstanden til katalysatoren er forskjellig fra den for de faktiske stoffene som reagerer med hverandre, er det en heterogen katalysator. Dette er også tilfelle med Haber-Bosch-prosessen, hvor finfordelt jern på en jernoksydbærer i fast form tjener som en katalysator i en reaksjonsgassblanding. Denne heterogene katalysatoren, også kjent som "kontakt", blir til under reaksjonen fra et annet materiale som tidligere ble introdusert i reaktoren, "katalysatorforløperen" eller " forløperkontakten ".
Jernkatalysator

Den heterogene jernkatalysatoren er en katalytisk veldig aktiv form av kroppssentrert kubisk α-jern og produseres ved kjemisk reduksjon fra en spesiell form for oksidert jern, magnetitt (Fe 3 O 4 ). Effekten av katalysatoren forsterkes av oksidiske promotorer som på forhånd er tilsatt magnetitten. Når det gjelder ammoniakk-syntese, inkluderer disse for eksempel aluminiumoksid , kaliumoksid , kalsiumoksyd og magnesiumoksid .
Produksjonen av den nødvendige magnetittkontakten krever en spesiell smelteprosess der råmaterialene som brukes må være fri for katalysatorgift og promotortilleggene må fordeles jevnt i magnetittsmelten. Rask avkjøling av magnetittsmelten, som har en temperatur på rundt 3500 ° C, danner den ønskede katalysatoren med høy aktivitet , noe som reduserer slitestyrken. Til tross for denne ulempen foretrekkes den raske avkjølingsmetoden ofte i praksis.
Den reduksjon av katalysator-forløperen magnetitt til α-jern er utført med syntesegass direkte i produksjonsanlegg. Reduksjonen av magnetitt skjer i utgangspunktet via nivået av wustite (FeO), slik at kontakt dannes med en kjerne laget av magnetitt, som er omgitt av et skall laget av wüstite. Den ytterligere reduksjonen av magnetitt- og wustittfasen fører til dannelsen av α-jern, som sammen med promotorene danner det ytre skallet. Prosessene som er involvert er komplekse og avhenger av reduksjonstemperaturen. Som uforholdsmessig wustitt ved lavere temperaturer i et jern og en magnetittfase er reduksjonen av magnetitt til jern Wüstit- og den dominerende prosessen ved høyere temperaturer.
Α-jernet danner primære krystallitter med en diameter på ca. 30 nanometer . Disse danner et bimodalt poresystem med pordiametre på rundt 10 nanometer, som skyldes reduksjon av magnetittfasen, eller fra 25 til 50 nanometer, som skyldes reduksjon av wüstite-fasen. Med unntak av koboltoksid reduseres ikke promotorene .
Når jernoksid reduseres med syntesegass, produseres vanndamp som et biprodukt. Denne vanndampen må tas i betraktning for optimal katalysatorkvalitet. Hvis dette kommer i kontakt med det finfordelte jernet, fører dette, spesielt i forbindelse med høye temperaturer, til for tidlig aldring av katalysatoren på grunn av omkrystallisering . Av denne grunn holdes damptrykket til vannet i gassblandingen som dannes under katalysatordannelsen så lavt som mulig, med verdier under 3 gm −3 . Av denne grunn utføres reduksjonen ved høy gassutveksling , lavt trykk og lave temperaturer. Den eksoterme ammoniakken formasjon sikrer en gradvis økning i temperatur.
Reduksjonen av fersk, fullt oksidert katalysator eller forløper til full kapasitet er nådd tar fire til ti dager. Wüstite-fasen er raskere enn magnetittfasen (Fe 3 O 4 ) og reduseres ved lavere temperaturer. Etter detaljerte kinetiske, mikroskopiske og røntgen spektroskopiske undersøkelser, kunne det demonstreres at wüstite er den første som konverterer til metallisk jern. Dette fører til en tetthet inhomogenitet (gradient) av jern (II) ionene , som et resultat av at de diffunderer fra magnetitten gjennom wustitten til grensesnittet og utfelles der som jernkjerner.
I teknisk praksis har forhåndsreduserte, stabiliserte katalysatorer fått en betydelig markedsandel . De har allerede den fullt utviklede porestrukturen , men har blitt oksidert igjen på overflaten etter produksjon og er derfor ikke lenger pyroforiske . Reaktiveringen av slike forhåndsreduserte katalysatorer tar bare 30 til 40 timer i stedet for de vanlige tidsperioder på flere dager. I tillegg til den korte oppstartstiden, har de ytterligere fordeler med sin høyere vannmotstand og lavere vekt.
Sammensetning av en kontakt | % Jern | % Kalium | % Aluminium | % Kalsium | % Oksygen |
---|---|---|---|---|---|
Volumkomposisjon | 40.5 | 0,35 | 2.0 | 1.7 | 53.2 |
Overflatesammensetning før reduksjon | 8.6 | 36.1 | 10.7 | 4.7 | 40,0 |
Overflatesammensetning etter reduksjon | 11.0 | 27.0 | 17.0 | 4.0 | 41.0 |
Katalysatorer annet enn jern
Siden den industrielle innføringen av Haber-Bosch-prosessen har det blitt gjort mange anstrengelser for å forbedre den, noe som resulterte i betydelige fremskritt. I forbedringen av katalysatoren for ammoniakk-syntese har det imidlertid ikke vært noen betydelig fremgang på lang tid siden 1920-tallet.
Som en del av søket etter egnede katalysatorer ble mange metaller testet intensivt: Forutsetningen for egnethet er dissosiativ adsorpsjon av nitrogen (nitrogenmolekylet må derfor deles i to nitrogenatomer under adsorpsjon). Samtidig må ikke bindingen av nitrogenatomer være for sterk, ellers vil de katalytiske evnene bli redusert (dvs. selvforgiftning ). Metallene i det periodiske elementet til venstre for jerngruppen viser en så sterk binding til nitrogen. Den tilhørende dannelsen av volum- eller overflatenitrider , for eksempel , gjør kromkatalysatorer ineffektive, de forgifter seg selv. Metaller til høyre for jerngruppen adsorberer derimot nitrogen i liten grad for å kunne aktivere tilstrekkelig nitrogen for ammoniakk syntese. Haber selv brukte opprinnelig osmium og uran som katalysatorer. Under katalyse reagerer uran og danner nitrid, og osmiumoksid er veldig sjeldent, flyktig og svært giftig.
På grunn av den relativt lave prisen, god tilgjengelighet, enkel behandling, levetid og aktivitet, ble jern til slutt valgt som katalysator. For en produksjonskapasitet på 1800 tonn per dag kreves for eksempel et trykk på minst 130 bar , temperaturer på 400 til 500 ° C og et reaktorvolum på minst 100 m³. I følge teoretiske og praktiske studier er muligheten for ytterligere forbedring av den rene jernkatalysatoren begrenset. Først i 1984 ble jernkatalysatoren modifisert av kobolt at den merkbart økte aktiviteten.
Andre generasjons katalysatorer
Katalysatorer basert på ruthenium viser høyere aktivitet ved sammenlignbare trykk og lavere temperaturer og blir derfor referert til som andre generasjon katalysatorer. Aktiviteten deres er sterkt avhengig av katalysatorstøtten og promotorene. Et stort antall stoffer kan brukes som bærere, i tillegg til karbon er disse magnesiumoksid, aluminiumoksid, zeolitter , spineller og bornitrid .
Rutheniumaktiverte kullkatalysatorer har blitt brukt industrielt siden 1992 i "KBR Advanced Ammonia Process" (KAAP, tysk om den videreutviklede ammoniakkprosessen i henhold til Kellogg, Brown og Root ). Karbonbæreren brytes delvis ned i metan , som kan reduseres ved en spesiell behandling av karbon ved 1500 ° C og dermed bidrar til å forlenge levetiden. I tillegg utgjør det fint spredte karbon en eksplosjonsfare . Av disse grunner og på grunn av sin lave surhet , har magnesiumoksid vist seg å være et godt alternativ. Bærere med sure egenskaper fjerner elektroner fra ruthenium, gjør det mindre reaktivt og binder uønsket ammoniakk til overflaten.
Katalysatorgift
Katalysatorforgiftninger reduserer katalysatorens aktivitet. De er enten en del av syntesegassen eller kommer fra urenheter i selve katalysatoren, sistnevnte spiller ikke en viktig rolle. Vann, karbonmonoksid, karbondioksid og oksygen er midlertidige katalysatorgift. Svovel - fosfor - arsen - og klor - forbindelser er permanente giftstoffer.
Kjemisk inerte komponenter i syntesegassblandingen, for eksempel edelgasser eller metan, er egentlig ikke katalysatorgift, men de akkumuleres gjennom sykliseringen av prosessgassene og reduserer dermed partialtrykket til reaktantene , noe som igjen har en negativ effekt på omdannelse.
Reaksjonsteknikk
Syntese forhold
Temperatur (° C) | K ekv |
---|---|
300 | 4,34 × 10 -3 |
400 | 1,64 × 10 −4 |
450 | 4,51 × 10 -5 |
500 | 1,45 × 10 −5 |
550 | 5,38 × 10 −6 |
600 | 2,25 × 10 −6 |
Ammoniakk-syntesen foregår med et nitrogen-til-hydrogen-forhold på 1 til 3, et trykk på 250 til 350 bar, en temperatur på 450 til 550 ° C og ved bruk av α-jern som katalysator i henhold til følgende ligning:
Reaksjonen er en eksoterm likevektsreaksjon som finner sted med en reduksjon i volum, hvis massehandlingskonstant K eq er resultatet av følgende ligning:
- .
Siden reaksjonen er eksoterm, forskyves likevekten i reaksjonen til siden av ammoniakken ved lavere temperaturer. Videre produserer fire volumdeler av råvarene to volumdeler ammoniakk. I samsvar med prinsippet om minst begrensning , favoriserer høyt trykk derfor også dannelsen av ammoniakk. Et høyt trykk er også nødvendig for å sikre at overflaten av katalysatoren er tilstrekkelig dekket med nitrogen.
Den ferritt (α-Fe) katalysator er produsert i reaktoren ved å redusere magnetitt med hydrogen. Dette er optimalt effektivt fra temperaturer på rundt 400 til 500 ° C. Aktiveringsbarrieren for spaltingen av nitrogenmolekylets trippelbinding reduseres kraftig av katalysatoren , men høye temperaturer er nødvendige for en tilstrekkelig reaksjonshastighet. Ved den valgte reaksjonstemperatur ligger det optimale mellom nedbrytningen av ammoniakk i utgangsmaterialene og effektiviteten til katalysatoren. Den dannede ammoniakken fjernes kontinuerlig fra reaksjonssystemet. Volumfraksjonen av ammoniakk i gassblandingen er rundt 20%.
De inerte komponentene, spesielt edelgassene som argon , må ikke overstige et visst innhold for ikke å senke partialtrykket til reaktantene for mye. For å fjerne de inerte gasskomponentene trekkes en del av gassen ut og argonen skilles fra i et gasseparasjonssystem . Ekstraksjon av rent argon fra syklusgassen er mulig ved hjelp av Linde-prosessen.
Storskala implementering
Moderne ammoniakkplanter produserer mer enn 3000 tonn per dag i en produksjonslinje. Diagrammet nedenfor viser strukturen til et Haber-Bosch-system.
Avhengig av opprinnelsen til syntesegassen, må den først frigjøres fra urenheter som hydrogensulfid eller organiske svovelforbindelser, som fungerer som katalysatorgift. Høye konsentrasjoner av hydrogensulfid, som forekommer i syntesegass fra ulmende koks , fjernes i et våtrengjøringstrinn som Sulphosolvan-prosessen , lave konsentrasjoner ved adsorpsjon på aktivt karbon . Organosvovelforbindelser skilles fra ved trykksvingadsorpsjon sammen med karbondioksid etter CO-omdannelsen.
For å produsere hydrogen ved hjelp av dampreformering av metan reagerer med vanndamp ved hjelp av en nikkel jernoksyd- aluminium- oksyd -katalysator i den primære reformeren for å danne karbonmonoksyd og hydrogen . Den energi som kreves for dette, entalpi Δ H , er 206 kJ / mol.
Metangassen omdannes bare delvis i den primære reformatoren. For å øke utbyttet av hydrogen og holde innholdet av inerte komponenter så lavt som mulig, blir den gjenværende metangassen omdannet med oksygen til karbonmonoksid og hydrogen i et andre trinn i den sekundære reformatoren . For dette formålet er den sekundære reformatoren ladet med luft, og nitrogenet som kreves for den påfølgende ammoniakk-syntesen kommer også inn i gassblandingen.
I et tredje trinn oksyderes karbonmonoksidet til karbondioksid, som er referert til som en CO-konvertering eller vanngassskiftreaksjon .
Karbonmonoksid og karbondioksid kombineres med ammoniakk for å danne karbamater som, som faste stoffer , raskt tetter rør og utstyr . I det følgende prosesstrinnet må karbondioksidet derfor fjernes fra gassblandingen. I motsetning til karbonmonoksid kan karbondioksid lett fjernes fra gassblandingen ved gassskrubbing med trietanolamin . Gassblandingen inneholder da også edelgasser som argon og metan, som er inerte .
Gassblandingen komprimeres deretter til ønsket driftstrykk ved hjelp av turbokompressorer . Den resulterende kompresjonsvarmen forsvinner ved hjelp av varmevekslere ; den brukes til å forvarme rå gasser.
Den faktiske produksjonen av ammoniakk foregår i ammoniakkreaktoren, hvorved de første reaktorene sprekker under høyt trykk, da atomhydrogenet i karbonstål delvis rekombineres til metan og sprekker stålet. Derfor utviklet Bosch rørreaktorer bestående av et trykkbærende stålrør der det ble satt inn et foringsrør laget av jern med lite karbon, hvor katalysatoren ble fylt. Hydrogen som diffunderer gjennom det indre stålrøret, slapp ut på utsiden gjennom tynne hull i den ytre stålkappen, de såkalte Bosch-hullene. Utviklingen av hydrogenbestandige krom-molybdenstål gjorde det mulig å konstruere enveggede rør. En ulempe med de rørformede reaktorene var det relativt høye trykktapet som måtte påføres på nytt ved kompresjon .
Moderne ammoniakkreaktorer er utformet som gulvreaktorer med lavt trykktap, der kontaktene fordeles som senger i omtrent ti etasjer over hverandre. Gassblandingen strømmer gjennom dem etter hverandre fra topp til bunn. Kald gass injiseres fra siden for kjøling. En ulempe ved denne typen reaktorer er den ufullstendige omdannelsen av den kalde gassblandingen i det siste katalysator-sjiktet.
Alternativt blir reaksjonsblandingen avkjølt mellom katalysatorlagene ved hjelp av varmevekslere, idet hydrogen-nitrogenblandingen er forvarmet til reaksjonstemperaturen. Reaktorer av denne typen har tre katalysatorsenger. I tillegg til god temperaturkontroll har denne typen reaktorer fordelen av bedre omdannelse av råstoffgassene sammenlignet med reaktorer med kald gasstilførsel.
Reaksjonsproduktet fjernes kontinuerlig for maksimalt utbytte. For dette formålet blir gassblandingen avkjølt fra 450 ° C i en varmeveksler ved bruk av vann, nytilførte gasser og andre prosessstrømmer. Ammoniakken kondenserer også og skilles i en trykkutskiller. De ennå ikke omdannede reaktantene nitrogen og hydrogen komprimeres igjen til reaksjonstrykk ved hjelp av en sirkulerende gasskompressor, supplert med fersk gass og mates til reaktoren. Ammoniakken renses i en påfølgende destillasjon.
Produkter
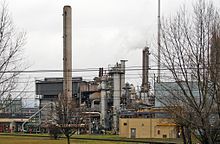
Det meste av ammoniakk som kreves årlig produseres ved hjelp av Haber-Bosch-prosessen. Den årlige produksjonen var på rundt 150 millioner tonn i 2017 med Kina , India og Russland som de største produsentene. På grunn av de høye energibehovene i produksjonen av det rene hydrogenet som kreves, utgjør Haber-Bosch-prosessen rundt 1,4 prosent av verdens energibehov . Karbondioksidutslippene som genereres i prosessen utgjør rundt tre til fem prosent av de globale utslippene, hvorav noen brukes til å generere urea. I dag, i det minste blant befolkningen i industrialiserte nasjoner, har rundt 40 prosent av nitrogenet i menneskekroppen allerede deltatt i Haber-Bosch-syntesen.
Cirka 80 prosent av primærproduktet ammoniakk blir bearbeidet til gjødsel, mens andre produkter utgjør 20 prosent. De viktigste ammoniakkbaserte nitrogengjødselene , i tillegg til de gassformige og vandige løsningene av ammoniakk, er ammoniumnitrat og urea .
Produksjonen av urea i høytrykksprosess går tilbake til Carl Bosch og Wilhelm Meiser og ble først satt i drift av BASF i 1922. I 2010 var produksjonsvolumet 130 millioner tonn. Hele verdensproduksjonen av salpetersyre foregår gjennom katalytisk forbrenning i henhold til Ostwald-prosessen . Prosessen går tilbake til et forelesningseksperiment der en glødende platinatråd blir nedsenket i en ammoniakk-luftblanding for å generere lystgasser . Verdens årlige produksjon var på 80 millioner tonn i 2009. Det hyppigst produserte biproduktet av salpetersyre er ammoniumnitrat ; den årlige produksjonen i 2002 var på rundt 39 millioner tonn, hvorav rundt 80 prosent blir bearbeidet til gjødsel og 20 prosent til eksplosiver. Andre sekundære produkter som kaliumnitrat , fosfater delvis eller fullstendig nøytralisert med ammoniakk, så som mono- , di- og ammoniumpolyfosfater , ammoniumsulfat og ammoniumnitrat-ureaoppløsning er ofte brukt gjødsel.
Cirka fem prosent av ammoniakkproduksjonen brukes til å lage sprengstoff. Nitro- og nitratgruppene som finnes i mange eksplosiver er til slutt basert på ammoniakk oppnådd ved hjelp av Haber-Bosch-prosessen, inkludert viktige eksplosiver som trinitrotoluen og nitroglyserin . Omtrent ti prosent av ammoniakkproduksjonen brukes til å lage nitrogenholdige forbindelser som nitriler , aminer og amider . Utvalget av sekundære produkter er ekstremt mangfoldig og spenner fra ureaharpikser , sulfonamider til nitrobenzen og dets sekundære produkt anilin i polyuretan- og fargestoffkjemi, kaprolaktam for produksjon av polymerer og til raketdrivstoff som hydrazin .
mekanisme
Elementære trinn
Mekanismen for ammoniakk-syntese er delt inn i følgende syv trinn:
- Transport av utgangsmaterialene fra gassfasen gjennom grenselaget til overflaten av kontakten
- Porediffusjon til reaksjonssenteret
- Adsorpsjon av reaktantene
- reaksjon
- Desorpsjon av produktene
- Retur av produktene gjennom poresystemet til overflaten
- Gå tilbake til gassvolumet.
På grunn av katalysatorens skallstruktur er de første og siste to trinnene raske sammenlignet med adsorpsjon, reaksjon og desorpsjon. Utvekslingsreaksjoner mellom hydrogen og deuterium på Haber-Bosch-katalysatorer finner sted med en målbar hastighet selv ved temperaturer på -196 ° C; Utvekslingen mellom deuterium og hydrogen på ammoniakkmolekylet skjer også ved romtemperatur . Siden begge trinnene er raske, kan de ikke bestemme hastigheten for ammoniakk-syntese. Det er kjent fra forskjellige studier at det hastighetsbestemmende trinn i ammoniakk-syntese er dissosiasjon av nitrogen.
Adsorpsjonen av nitrogen på katalysatoroverflaten avhenger ikke bare av reaksjonsbetingelsene, men også av den mikroskopiske strukturen til katalysatoroverflaten. Jern har forskjellige krystallflater , hvis reaktivitet er veldig forskjellig. Den Fe (111) og Fe (211) flater har langt den høyeste aktivitet. Forklaringen på dette er at bare disse overflatene har såkalte C7-steder - dette er jernatomer med syv nærmeste naboer.
Den dissosiative adsorpsjonen av nitrogen på overflaten følger følgende skjema, der S * betyr et jernatom på overflaten av katalysatoren:
- N 2 → S * –N 2 (γ-art) → S * –N 2 –S * (α-art) → 2 S * –N (β-art, overflatenitrid )
Adsorpsjonen av nitrogen er lik kjemisorpsjonen av karbonmonoksid. På et Fe (111) overflate, adsorpsjon av nitrogen i første omgang fører til en adsorbert y-arter med en adsorpsjon energi på 24 kJmol -1 og en NN strekker vibrasjon på 2100 cm -1 . Siden nitrogen er isoelektronisk med karbonmonoksid , adsorberes det i en endelig konfigurasjon der molekylet er bundet via et nitrogenatom vinkelrett på metalloverflaten. Dette ble bekreftet med fotoelektronspektroskopi .
Ab initio - MO- beregninger har vist at i tillegg til σ-Hinbindung er det eneste paret av nitrogen til metallet en π tilbake-donasjon fra d-orbitalene tilstede metallet i π * orbitalene til nitrogenet som inneholder jern- nitrogen Bond styrker. Nitrogen i α-tilstand er sterkere bundet med 31 kJmol −1 . Den resulterende svekkelsen av NN-bindingen kan demonstreres eksperimentelt ved å redusere bølgetallet til NN-strekkvibrasjonen til 1490 cm -1 .
Ytterligere oppvarming av Fe (111) overflate, som er dekket av α-N- 2 , fører til både desorpsjon og tilsynekomst av en ny bånd ved 450 cm -1 . Dette representerer en metall-N-svingning, β-tilstanden. En sammenligning med den vibrasjonsspektra av komplekse forbindelser tillater den konklusjon at den N- 2- molekylet er bundet til “side-on”, med et N-atom i kontakt med en C7-område. Denne strukturen kalles "overflatenitrid". Overflatens nitrid er veldig sterkt bundet til overflaten. Hydrogenatomer (H- annonser ), som er veldig mobile på katalysatoroverflaten , legger raskt til dette.
Overflate imider (NH ad ), overflate amider (NH 2, ad ) og overflate ammoniaates (NH 3, ad ), som blir detektert ved infrarød spektroskopi , er dannet, den sistnevnte desintegrerende med frigivelse av NH 3 (desorpsjon). De individuelle molekylene ble identifisert eller tildelt ved hjelp av røntgenfotoelektron-spektroskopi (XPS), høyoppløselig elektronenergitapsspektroskopi (HREELS) og IR-spektroskopi.
På grunnlag av disse eksperimentelle resultatene kan det opprettes et reaksjonsskjema som består av følgende individuelle trinn:
- H 2 + S * ⇌ 2 H ad
- N 2 + S * ⇌N 2, ad
- N 2, annonse ⇌ 2 N annonse
- N ad + H ad ⇌ NH ad
- NH ad + H ad ⇌ NH 2, ad
- NH 2, ad + H ad ⇌ NH 3, ad
- NH 3, ad ⇌ NH 3 + S *
Som med alle Haber-Bosch-katalysatorer, er det hastighetsbestemmende trinnet i ruthenium-aktivert karbon katalysatorer nitrogen dissosiasjon. For ruthenium, er det aktive sentret en såkalt B 5 område, en 5-gangers koordinert stilling på Ru (0001) overflate, ved hvilken to ruthenium-atomer danner en trinnkant med tre ruthenium-atomer på den Ru (0001) overflate. Antallet av B- 5 posisjoner avhenger av størrelsen og formen på partiklene ruthenium-, ruthenium forløperen og mengden av ruthenium anvendes. Den forsterkende effekten av den basiske bæreren har samme effekt som promotereffekten av alkalimetaller , som er like viktig her som med jernkatalysatoren.
Energidiagram
Med kunnskapen om reaksjonshalpien til de enkelte trinn, kan det opprettes et energidiagram . Ved hjelp av energidiagrammet kan man sammenligne homogene og heterogene reaksjoner: På grunn av den høye aktiveringsenergien ved dissosiasjon av nitrogen, kan den homogene gassfasereaksjonen ikke utføres. Den katalysator som unngår dette problemet, siden energigevinst som resulterer fra bindingen av nitrogenatomene til katalysatoroverflaten overcompensates for den nødvendige dissosiasjon energi, slik at reaksjonen er slutt eksoterm . Likevel forblir den dissosiative adsorpsjonen av nitrogen det hastighetsbestemmende trinn: ikke på grunn av aktiveringsenergien, men hovedsakelig på grunn av den ugunstige preeksponensielle faktoren til hastighetskonstanten. Den hydrogenering er endoterm, men denne energien kan lett påføres ved reaksjonstemperaturen (ca. 700 K).
Prosessvarianter
Siden introduksjonen av Haber-Bosch-prosessen har syntesen av ammoniakk fra atmosfærisk nitrogen blitt en av verdens viktigste kjemiske produksjonsprosesser. Utviklingen av prosessvarianter på begynnelsen av 1900-tallet tjente ofte til å omgå BASFs patentkrav. Siden prosessen krever betydelig energiforbruk , fokuserte senere utvikling på energieffektivitet . Det gjennomsnittlige energiforbruket per tonn ammoniakk i 2000 var rundt 37,4 GJ, mens det termodynamisk bestemte minimum er 22,4 gigajoules per tonn.
Casale metode
Den Casale prosessen ble utviklet av Luigi Casale i begynnelsen av 1920-tallet . Prosessen bruker en jernkatalysator, men fungerer i kontrast til Haber-Bosch-prosessen med et trykk på rundt 800 til 1000 bar. Dette gjorde reaktoren mindre og tillot god temperaturkontroll gjennom en intern, sentral varmeveksler og aksial injeksjon av kald gass.
Det høye driftstrykket tillot direkte kondensering av ammoniakk uten opptak i vann. I 1923 hadde Casale bygget 15 fabrikker i Europa og USA med en kapasitet på rundt 80.000 tonn ammoniakk per år. I 1927 var den installerte kapasiteten allerede 320.000 tonn per år. På den tiden var Casale den eneste konkurrenten til BASF. Totalt er det bygget over 200 ammoniakkanlegg basert på den første generasjonen av Casale-teknologi over hele verden.
Fauser-metoden
Den Fauser prosessen , oppkalt etter den italienske elektroingeniør Giacomo Fauser , i stor grad samsvarer med Haber-Bosch-prosessen, men anvendes elektrolyse av vann som en hydrogenkilde. Fauser-cellen brukte 27% styrke kaliumhydroksydoppløsning som elektrolytt og asbest lukkede anoder og katoder , noe som sørget for en god separasjon av de resulterende gassene. Prosessen ble introdusert av Montecatini tidlig på 1920-tallet .
Mont Cenis-metoden
The Mont Cenis prosessen ble utviklet av Friedrich Uhde og først satt i drift i 1926 på Mont Cenis colliery . Prosessen, også kjent som lavtrykksprosessen, fungerer ved trykk på 80 til 90 bar og en temperatur på 430 ° C. Katalysatoren som ble brukt var en jerncyanid-aluminiumoksydkatalysator, som var mer aktiv enn katalysatoren utviklet av Mittasch. De mildere prosessforholdene gjorde det mulig å bruke billigere stål til konstruksjon av reaktorene.
AMV-prosedyre
Imperial Chemical Industries utviklet AMV-prosessen i 1982 med en svært aktiv jern-koboltkatalysator som fungerer ved et reaksjonstrykk på 100 bar og en temperatur på 380 ° C. Kobolt i seg selv er neppe katalytisk aktivt, men tjener til å stabilisere kontakten gjennom dannelse av spinelfaser med aluminiumoksydet. I tillegg dannes mindre jernkrystallitter med høyere aktivitet når kontakten reduseres.
En videre utvikling av prosessen er LCA-prosessen (Leading Concept Ammonia) utviklet av ICI i 1988, som er designet for lavere gjennomstrømninger med samme energiinngang. Karbondioksydet, som produseres i en-trinns vann-gass skiftreaksjon, fjernes ved hjelp av trykksving adsorpsjon .
Kellogg Advanced Ammonia Process
I 1992 utviklet MW Kellog en ruthenium-on-aktivert karbonkatalysator som fungerer ved lavere trykk og temperaturer under navnet Kellogg Advanced Ammonia Process (KAAP). Trykket som kreves er bare ca. 40 bar på grunn av den mer aktive, men dyrere ruthenium-katalysatoren. Alkali- eller jordalkalimetaller som cesium og barium brukes som promotorer . Katalysatoren sies å være omtrent 10 til 20 ganger så aktiv som den konvensjonelle jernkatalysatoren.
Solid State Ammonia Synthesis Process
I faststoff- ammoniakk- synteseprosessen (SSAS-prosess, fast-tilstand-ammoniakk- synteseprosess ) forbi den direkte elektrolytiske syntesen av ammoniakk fra vann og nitrogen ved hjelp av elektrisk energi omkjøringen via hydrogenproduksjon fra vann. Dette øker effektiviteten. Dannelsen av ammoniakk skjer elektrokjemisk i henhold til følgende ligning:
Reaksjonens bruttoligning er:
Siden ammoniakk er et høyt energi stoff, kreves det mye elektrisk energi. Denne prosessen er derfor bare økonomisk hvis veldig billig elektrisk energi er tilgjengelig.
weblenker
litteratur
- Gerhard Ertl : Elementære trinn i heterogen katalyse. I: Angewandte Chemie . 102, nr. 11, 1990, s. 1258-1266, doi: 10.1002 / ange.19901021108 .
- Hans-Erhard Lessing : Bread for the World, Death to the Enemy. i: Stephan Leibfried et al. (Hg): Berlins Wilde Energies - portretter fra historien til Leibniz Science Academy. de Gruyter, Berlin, 2015, ISBN 978-3-11-037598-5
- Sandro Fehr: "Nitrogenspørsmålet" i den tyske krigsøkonomien under første verdenskrig og rollen som nøytralt Sveits . Nordhausen 2009, DNB 993295185 .
- Alwin Mittasch : Historie om ammoniakk-syntesen. Verlag Chemie, Weinheim 1951, DNB 453395902 .
- Robert Schlögl : Katalytisk ammoniakk-syntese - en "uendelig historie"? I: Angewandte Chemie. 115, nr. 18, 2003, s. 2050-2055, doi: 10.1002 / anie.200301553 .
- Gerhard Ertl, Jens Soentgen : N: Nitrogen - an element makes world history. oekom Verlag, 2015, ISBN 978-3-86581-736-5 .
- Maks appl: ammoniakk. Prinsipper og industriell praksis. Wiley-VCH, Weinheim 1999, ISBN 3-527-29593-3 .
- Dietrich Stoltzenberg: Fritz Haber, Carl Bosch og Friedrich Bergius - hovedpersoner i høytrykkssyntese . I: Kjemi i vår tid . teip 33 , nei 6 , 1999, s. 359-364 , doi : 10.1002 / ciuz.19990330607 .
Individuelle bevis
- ↑ a b Nitrogen (fast) - ammoniakk. US Geological Survey, Mineral Commodity Summaries, januar 2018.
- ^ Vaclav Smil: Nitrogensyklus og verdens matproduksjon. (PDF) World Agriculture 2. 9-1., 2011, åpnet 20. februar 2019 (engelsk).
- ^ Fritz Haber: Minnetale om Justus von Liebig. I: Tidsskrift for anvendt kjemi. 41, 1928, s. 891-897, doi: 10.1002 / anie.19280413302 .
- ↑ a b c d e f g h Max Appl: Ammoniakk. I: Ullmann's Encyclopedia of Industrial Chemistry. Wiley-VCH Verlag, 2006, s. 11-13, doi: 10.1002 / 14356007.a02 143.pub2
- ^ William Crookes: Presidentens tale før British Association for the Advancement of Science, Bristol, 1898. I: Science. 1898, s. 561-575, doi: 10.1126 / science.8.200.561
- ^ William Crookes: Hveteproblemet. Longmans, Green og Co., London / New York / Bombay / Calcutta 1917.
- ↑ a b A. Hermann: Haber og Bosch: Bread from Air - Ammoniakk-syntesen. I: Physics Journal. 21, 1965, s. 168-171, doi: 10.1002 / phbl.19650210403
- ^ Nicodem Caro: Industri av kalsiumcyanamid og relaterte prosesser. I: Tidsskrift for anvendt kjemi. 22, 1909, s. 1178-1182, doi: 10.1002 / anie.19090222404
- ↑ John R. Anderson: Katalyse: Vitenskap og teknologi. Verlag Springer, 1990, ISBN 3-642-64666-2 , s. 48.
- ↑ Hans-Erhard Lessing: Bread for the World, Death to the Enemy. i S. Leibfried (Hg): Berlins Wilde Energien de Gruyter, Berlin, 2015 s. 349
- ^ Thomas Hager: The Alchemy of Air: A Jewish Genius, a Doomed Tycoon, and the Scientific Discovery That Fed the World but Drived the Rise of Hitler. Utgiver Crown, 2008, ISBN 978-0-307-35178-4 , s.96 .
- ↑ Kristian Birkeland: Om oksidasjon av atmosfærisk nitrogen i elektriske buer. I: Transaksjoner fra Faraday Society. 2, 1906, s. 98-116, doi: 10.1039 / tf9060200098
- Itz Fritz Haber, G. van Oordt: Om dannelsen av ammoniakk i elementene. I: Journal of Inorganic Chemistry. 44, 1905, s. 341-378, doi: 10.1002 / zaac.19050440122
- ↑ Patent US971501 : Produksjon av ammoniakk. Publisert 27. september 1910 , oppfinnere: Fritz Haber, Robert Le Rossignol.
- ↑ Patent DE235421A : Fremgangsmåte for syntetisk fremstilling av ammoniakk fra grunnstoffene. Publisert 13. oktober 1908 .
- ^ A b c d Carl Bosch: Utviklingen av den kjemiske høytrykksmetoden under etableringen av den nye ammoniakkindustrien. Tale for tildeling av Nobelprisen 21. mai 1932.
- ↑ Armin Hermann, Charlotte Schönbeck (red.): Teknologi og vitenskap (teknologi og kultur). Springer, 1991, ISBN 3-540-62259-4 , s. 441-442.
- ↑ Manfred Baerns, Arno Behr, Axel Brehm: Teknisk kjemi. Lærebok . Wiley-VCH, 2006, ISBN 3-527-31000-2 , s. 623.
- ↑ a b Alwin Mittasch: Kommentarer til katalyse. I: Rapporter fra German Chemical Society (A- og B-serien). 59, 1926, s. 13-36, doi: 10.1002 / cber.19260590103
- ↑ Werner Abelshauser, Wolfgang von Hippel, Jeffrey Alan Johnson: The BASF. Fra 1865 til i dag. CH Beck Verlag, 2002, ISBN 3-406-49526-5 , s. 171.
- ↑ David Turnock: Østeuropeisk økonomi, 1800-1989: Transformasjonsstadier i en perifer region. Routledge Chapman & Hall, 2005, ISBN 1-4039-3287-5 , s. 197.
- ^ Harm G. Schröter: Det internasjonale nitrogenkartellet 1929-1939. I: Harm G. Schröter, Clemens A. Wurm (red.): Politikk, økonomi og internasjonale relasjoner, studier om deres forhold i perioden mellom verdenskrigene . Mainz 1991, ISBN 3-8053-1255-5 , s. 129-130.
- ^ A b Vaclav Smil: Enriching the Earth: Fritz Haber, Carl Bosch, and the Transformation of World Food Production. MIT Press, 2001, ISBN 0-262-69313-5 , s. 242.
- ↑ Wolfgang Zollitsch: Arbeidere mellom den store depresjonen og nasjonalsosialismen: et bidrag til samfunnshistorien i årene 1928 til 1936. Vandenhoeck & Ruprecht, 1990, ISBN 3-525-35751-6 , s. 22-24.
- ^ Hans-Erhard Lessing: Robert Bosch. Rowohlt, Reinbek nær Hamburg, 2007, ISBN 978-3-499-50594-2 , s. 142.
- ^ Nitrogen (Fixed) - Ammonia - Supply-Demand Statistics. US Geological Survey, Historical Statistics for Mineral and Material Commodities in the United States, Data Series 140, 2015.
- ↑ a b c d Roman J. Press et al.: Introduksjon til hydrogenteknologi . John Wiley & Sons, 2008, ISBN 978-0-471-77985-8 , s. 99-125.
- ↑ Patent US2083795 : Produksjon av hydrogen. Publisert 15. juni 1937 , oppfinnere: Georg Schiller, Gustav Wietzel.
- ↑ Vaclav Smil: Enriching the Earth: Fritz Haber, Carl Bosch, and the Transformation of World Food Production. MIT Press, 2001, ISBN 0-262-69313-5 , s. 113.
- ↑ Fangming Jin (Ed.): Bruk av Hydrotermale Reaksjoner på Biomasse konvertering. Springer, 2014, ISBN 978-3-642-54457-6 , s. 221.
- ↑ Friedrich Asinger: Introduksjon til petrokjemi . Akademie-Verlag, Berlin 1959, s. 138.
- ↑ a b c d e f g h i Max Appl: Ammoniakk. Prinsipper og industriell praksis . Wiley-VCH, Weinheim et al. 1999, ISBN 3-527-29593-3 , pp. 17–64 ( begrenset forhåndsvisning i Google Book Search).
- ↑ WK Jozwiak, E. Kaczmarek et al.: Reduksjonsatferd av jernoksider i hydrogen- og karbonmonoksidatmosfærer. I: Anvendt katalyse A: Generelt. 326, 2007, s. 17-27, doi: 10.1016 / j.apcata.2007.03.021
- ↑ Gerhard Ertl: Til mekanismen for ammoniakk-syntese. I: Nyheter fra kjemi, teknologi og laboratoriet. 31, 1983, s. 178-182, doi: 10.1002 / nadc.19830310307
- ↑ Michael Bowker: PhD i ammoniaksyntese . I: DA King, DP Woodruff (red.): Kjemisk fysikk av faste overflater . Volum 6: Koadsorpsjon, promotorer og gift . Elsevier, 1993, ISBN 0-444-81468-X , kapittel 7, s. 225-268 .
- ↑ a b c d Zhixiong You, Koji Inazu, Ken-ichi Aika, Toshihide Baba: Elektronisk og strukturell promotering av bariumheksaaluminat som en rutheniumkatalysatorstøtte for ammoniakk-syntese . I: Journal of Catalysis . teip 251 , nr. 2. oktober 2007, doi : 10.1016 / j.jcat.2007.08.006 .
- ↑ F. Rosowski, A. Hornung, O. Hinrichsen, D. Herved M. Muhler: ruthenium-katalysatorer for ammoniakksyntese ved høyt trykk: Fremstilling, karakterisering, og strøm-lov-kinetikk . I: Anvendt katalyse A: Generelt . teip 151 , nr. 2. april 1997, doi : 10.1016 / S0926-860X (96) 00304-3 .
- ↑ a b Jürgen Falbe: Römpp-Lexikon Chemie (H - L) , Georg Thieme Verlag, 1997, ISBN 3-13-107830-8 , s. 1644–1646.
- ^ Theodore L. Brown, H. Eugene LeMay, Bruce Edward Bursten, Linda Sue Brunauer (red.): Chemistry the Central Science. 9. utgave. Prentice Hall, Upper Saddle River, NJ 2003, ISBN 0-13-038168-3 .
- ↑ a b c A. F. Holleman , E. Wiberg , N. Wiberg : Textbook of Inorganic Chemistry . 102. utgave. Walter de Gruyter, Berlin 2007, ISBN 978-3-11-017770-1 , s. 662-665.
- ↑ Boy Cornils, Wolfgang A. Herrmann, M. Muhler, C. Wong: Catalysis from A to Z: A Concise Encyclopedia. Verlag Wiley-VCH, 2007, ISBN 978-3-527-31438-6 , s.31 .
- ↑ Fokus på kjemi øverste nivå innledende fase. Cornelsen-Verlag, Berlin 2010, ISBN 978-3-06-013953-8 , s. 79.
- ↑ P. Häussinger et al.: Noble Gases. I: Ullmann's Encyclopedia of Industrial Chemistry. Wiley-VCH, Weinheim 2006, doi : 10.1002 / 14356007.a17_485
- Le E. Leibnitz, H. Koch, A. Götze: Om trykkløs prosessering av brunkullkoksovnsgass til sterk gass i henhold til Girbotol-prosessen. I: Tidsskrift for praktisk kjemi. 13, 1961, s. 215-236, doi: 10.1002 / prac.19610130315
- ↑ a b Dirk Steinborn: Grunnleggende om organometallisk kompleks katalyse. Teubner, Wiesbaden 2007, ISBN 978-3-8351-0088-6 , s. 319-321.
- ^ A b c Detlef Forst, Maximillian Kolb, Helmut Roßwag: Kjemi for ingeniører. Springer Verlag, 1993, ISBN 3-662-00655-3 , s. 234-238.
- Hef Patrick Heffer, Michel Prud'homme: Gjødselutsikter 2010–2014. I: 78. IFA Årskonferanse, Paris. 31. 2010, s.6.
- Este Celeste LeCompte: Gjødselanlegg springer opp for å dra nytte av USAs billige naturgass. I: Scientific American. 2013. (online)
- ↑ TE Crews, MB Peoples: Belgfrukter versus gjødselkilder til nitrogen: økologiske avveininger og menneskelige behov. I: Landbruk, økosystemer og miljø. 102, 2004, s. 279-297, doi: 10.1016 / j.agee.2003.09.018 .
- ↑ Jan Willem Erisman, Mark A. Sutton, James Galloway, Zbigniew Klimont, Wilfried Winiwarter: Hvordan et århundre med ammoniakksyntese forandret verden. I: Nature Geoscience. 1, 2008, s. 636-639, doi: 10.1038 / ngeo325
- ↑ Patent US1429483 : Fremstillingsprosess for urea. Publisert 19. september 1922 , oppfinnere: Carl Bosch, Wilhelm Meiser.
- ↑ a b c d e M. Bertau, A. Müller, P. Fröhlich, M. Katzberg: Industrielle Inorganische Chemie , 2013, Wiley-VCH, ISBN 978-3-527-33019-5 , s. 31-37.
- ↑ Dirk Steinborn: Grunnleggende om organometallisk kompleks katalyse. Teubner, Wiesbaden 2007, ISBN 978-3-8351-0088-6 , s.7 .
- ↑ Allen V. Barker, David J. Pilbeam (Eds.): Handbook of Plant Nutrition . CRC Press, 2006, ISBN 0-8247-5904-4 , s. 40.
- ↑ Jacqueline Akhavan: Kjemi av eksplosiver . Royal Society of Chemistry, 2011, ISBN 978-1-84973-330-4 , s. 44-46.
- ^ AF Holleman , E. Wiberg , N. Wiberg : Lærebok for uorganisk kjemi . 102. utgave. Walter de Gruyter, Berlin 2007, ISBN 978-3-11-017770-1 , s. 675-680.
- ^ Walter J. Moore, Dieter O. Hummel: Fysisk kjemi . Walter de Gruyter, Berlin 1983, ISBN 3-11-008554-2 , s. 604.
- ↑ G. Ertl, SB Lee, M. Weiss: Kinetikk av nitrogen adsorpsjon på Fe (111). I: Surface Science. 114, 1982, s. 515-526, doi: 10.1016 / 0039-6028 (82) 90702-6 .
- ↑ a b SB Lee, M. Weiss: Adsorpsjon av nitrogen på kaliumfremmede Fe (111) og (100) overflater . I: Surface Science . teip 114 , nr. 2-3 , februar 1982, s. 527-545 , doi : 10.1016 / 0039-6028 (82) 90703-8 .
- ↑ a b Gerhard Ertl: Reaksjoner på faste overflater . John Wiley & Sons, 2010, ISBN 978-0-470-26101-9 , pp. 123 ( begrenset forhåndsvisning i Google Book-søk).
- ↑ Jeppe Gavnholt, Jakob Schiøtz: Struktur og reaktivitet av ruthenium nanopartikler. I: Physical Review B. 77, 2008, doi: 10.1103 / PhysRevB.77.035404 .
- ^ J. Ruddock, TD Short, K. Brudenell: Energintegrasjon i ammoniakkproduksjon. I: WIT Transactions on Ecology and the Environment. 62, 1970, doi: 10.2495 / EENV030251 .
- ↑ James A. Kent (red.): Kent og Riegels håndbok for industriell kjemi og bioteknologi . Verlag Springer, 2007, ISBN 978-0-387-27842-1 , s. 998-999.
- ↑ Patent US1478550 : Katalytisk apparat for syntese av ammoniakk. Publisert 25. desember 1923 , oppfinner: Luigi Casale.
- ^ A b Casale SA: Ammoniakk - Utvikling av teknologi. Hentet 27. juni 2016.
- ↑ Patent US1495681 : Elektrolysator for produksjon av hydrogen og oksygen. Publisert 27. mai 1924 , oppfinner: Giacomo Fauser.
- ↑ Jean Billiter: Teknisk elektrolyse av ikke-metaller. Verlag Springer, 1954, ISBN 978-3-7091-5728-2 , s. 42-44.
- ↑ Bernhard Neumann (red.): Lærebok for kjemisk teknologi og metallurgi: I Fuels Uorganic branches of industry. Verlag Julius Springer, 1939, ISBN 978-3-642-92056-1 , s. 408-409.
- ↑ Huazhang Liu: Ammoniak- syntesekatalysatorer : innovasjon og praksis . World Scientific Pub., 2013, ISBN 978-981-4355-77-3 , s. 739-740.
- R JR Jennings: Katalytisk ammoniaksyntese. Grunnleggende og praksis. Springer Science and Business Media, 1991, ISBN 1-4757-9594-7 , s. 353.
- ^ Gary Maxwell: Syntetiske nitrogenprodukter: En praktisk guide til produktene og prosessene. Verlag Springer, 2004, ISBN 0-306-48225-8 , s. 181-182.
- ^ Anne K. Rhodes: Ny ammoniakkprosess, katalysator bevist i kanadisk anlegg. I: Oil and Gas Journal. 47, 1996 (online)
- ↑ Hubert Bielawa, Olaf Hinrichsen, Alexander Birkner, Martin Muhler: Ammoniak- syntesekatalysatoren til neste generasjon: Bariumfremmet oksidstøttet ruthenium. I: Angewandte Chemie International Edition. 40, 2001, s. 1061-1063, doi : 10.1002 / 1521-3773 (20010316) 40: 6 <1061 :: AID-ANIE10610> 3.0.CO; 2-B .
- ^ Rong Lan, John TS Irvine, Shanwen Tao: Syntese av ammoniakk direkte fra luft og vann ved omgivelsestemperatur og trykk. I: Vitenskapelige rapporter. 3, 2013, doi: 10.1038 / srep01145 .