Masovn
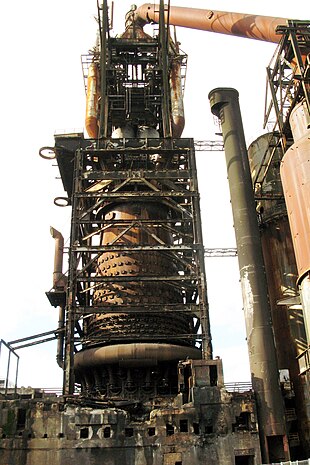

En masovn (også foreldet Hohofen ) er en stor-skala anlegg med hvilken flytende råjern som blir produsert fra bearbeidet jernmalmer (hovedsakelig oksyder ) i en kontinuerlig reduksjon og smelting .
Hele anlegget er også kjent som jernverk eller smelteverk og har i tillegg til masovnen som den sentrale komponenten andre fasiliteter som sørger for kontinuerlig drift. Disse inkluderer bunkeren for lagring av inngangsmaterialene ( Möller : jernmalm og tilslag ) og oppvarmingsmaterialene ( koks ) med tilkoblede transport- og rørsystemer for å bringe dem inn i ovnhodet ved ovnhodet. Ytterligere anordninger tjener til å utlade ovnsgassen ved ovnens hode, for å forsyne den blåseren vinden forvarmes av den masovn i den midtre del av masovnen og til utløps råjern og slagg i ovnen basen.
Tilsetningsstoffene i Möller , slik som silisiumdioksid (kvartssand) , kalsiumoksid (kalk) og andre, brukes under masovnsprosessen for å binde malmens uønskede bestanddeler i slaggen og også senke smeltetemperaturen til jern . Koks som påføres i lag fungerer som energibærer og reduksjonsmiddel, og den varme vinden som blåses inn gjennom flere tuyer leverer nødvendig oksygen .
En del av karbonet og det meste av fosfor og svovel som har blitt absorbert, må deretter fjernes fra råjernet som er produsert ved raffinering før det kan viderebehandles til forskjellige typer støpejern eller stål . Slagg og ovngass produseres som biprodukter . Slaggen blir vanligvis granulert og brukt som slagg i sementindustrien. Med ovngassen genereres først den nødvendige varmeeksplosjonen, deretter brukes den som oppvarmingsgass.
Den moderne masovnen prosess utviklet i løpet av rundt 5000 år fra enkle racing eller klump branner, drevet med kull og viftet med kald luft, i racing ovner og stykke ovner . Prosessen skiller seg betydelig fra den moderne masovnen. De klassiske ovnene bruker direkte reduksjon for å produsere solid smijern med lavt karboninnhold. Bare flytende slagg renner ut av ovnen. Rasejernet kunne og måtte deretter smides for å kunne drive ut den fangede slaggen. I motsetning til dette, må grisejernet produsert med flåteovnen og påfølgende masovn, som har blitt oppvarmet med koks fra begynnelsen av 1700-tallet og drives med varmblåsing siden 1828, avkolkes i et ytterligere arbeidstrinn.
Produksjonen av ett tonn stål produserer rundt 1,37 tonn av klimagassen CO 2 , en stor del av den i masovnsprosessen. I Tyskland tilsvarer dette rundt en tredjedel av industrielle utslipp. Mange store stålbedrifter i Europa planlegger derfor å erstatte masovnsprosessen med lavutslippsprosesser som direkte reduksjon med hydrogen , og dermed nærme seg den klassiske prosessen igjen.
historie
For tidligste bruk og arkeologiske funn av jern se
Begynnelsen av jernsmelting i Europa

En av de første enkle og lenge brukte former for jernsmelting var den såkalte racingbrannen (også kjent som Luppenfeuer ). En traktformet grop med en diameter på omtrent 30 centimeter ble fylt med kull og lett reduserbar jernmalm , antennet og forsynt med atmosfærisk oksygen fra en halvkuleformet, pelsdekket bolle (en tidlig form av belgen ) som fungerer som en vifte . Etter omtrent ti timer, det var en neve stor, svart, med jernmalmkorn og uforandret eller på bakken slagg taket Luppe ( jernsvamp akkumulert). Under ovnsreisen flytes ikke jernet i en racingovn. Temperaturene som kreves for dette kan nås uten problemer, men produktet som oppnås på denne måten ville være kraftig karburisert og ikke lenger smidig. Under drift måtte temperaturen derfor holdes permanent i et område som ikke tillot metallet å flyte. Racingovnen , hovedsakelig laget av leire eller steiner, var en videreutvikling av racingbrannen med en sideåpning for lufttilførselen og en kort aksel for å fylle og fylle på med kull før og under ovnen. Skaftet støttet også den naturlige skorsteinseffekten , slik at temperaturer mellom 1000 og 1200 ° C kunne nås. Lufttilførselen ble først utført med naturlig trekk, for eksempel ved å bygge på en voll , og ovnene ble derfor betegnet som vindovner eller utkast ovner . I tilfelle av vifteovnene , derimot, sikret belgen en mer effektiv og kontrollert lufttilførsel. Avhengig av varigheten av ovnssyklusen (4 til 20 timer) og avhengig av størrelsen på ovnen, fikk de tidlige jernarbeiderne en fille med en vekt på noen få kilo til flere hundrevekt . Dette ble deretter frigjort for kull og slagg ved gjentatt oppvarming (forvarming) og smiing , komprimert og - for det meste ved bruk av halvfabrikata - bearbeidet til de ønskede arbeidsemnene.
Se også: Jernproduksjon i Lahn-Dill-området og jernsmelting blant de germanske folkene .
Racingovner med festede smier, såkalte racingverk, var fremdeles utbredt frem til 1700-tallet. De ansatte omtrent fem til ti mann og produserte omtrent 60 til 120 tonn dukker i året. 2,7 kilo kull ble brent per kilo jern .
Utvikling av masovnen
Selv om racingovnen ble brukt i lang tid på grunn av sin enkle konstruksjon, begynte kraftigere ovner å bli utviklet så tidlig som på begynnelsen av 1200-tallet. Den stykke ovn (også kjent som "ulv ovn"), som ble oppkalt etter stykke jern som ble tatt ut av ovnen, kan ses som en link til utviklingen av dagens masovner . Ovnen var en firkantet murstein, skaftovn med åpen topp , hvis størrelse vokste fra rundt fire meter i høyden på slutten av middelalderen til ti meter i høyden på 1600-tallet, for eksempel stykkerovnene i Vordernberg i Steiermark , en senter for produksjon av råjern i Sentral-Europa på den tiden. De belgene i ovnene ble drevet av vannhjul og systemene er derfor også referert til som hjulet arbeider . De nådde temperaturer opp til 1600 ° C; blandingen av jernmalm og kull ble delvis smeltet. En videre utvikling var den blå ovnen, hvis navn stammer fra en korrupsjon av det engelske ordet blow (= to blow). I prinsippet tilsvarer den stykeovnen, men har en lukket ovnfront.
I smia ble imidlertid bare svampjernet (lappene) som hadde samlet seg over jernbadet, først behandlet, som nådde en slik størrelse i stykkerovnene at det ikke lenger ble bearbeidet for hånd, men med smiehammer også drevet av vann kraft . Det smeltede grisejernet som ble produsert ved smelteprosessen fremsto opprinnelig for smelteverkene som "rått jern" som ikke kunne brukes fordi det hadde absorbert en så høy andel karbon at det var for sprøtt for smiing. Det ble kalt Saueisen i Tyskland og Graglach , slamstrøm i Steiermark og støpejern i den engelskspråklige verden.
Problemet ble bare løst med oppfinnelsen av forskjellige prosesser for raffinering av jernet, rundt 1300-tallet. Dette banet også vei for ytterligere å øke effektiviteten til ovnene. Flåteovner ble bygget med flere meter tykke murverk, hvis ramme ble innsnevret, og hvor grisejernet ( mildt jern og mildt stål ) og slaggen som ble produsert etter at smelteprosessen ble avsluttet, ble drenert sammen. Flåteovner kan sees på som de umiddelbare "forfedrene" til masovnen, siden i prinsippet ingenting endret seg i jernutvinningsprosessen etter deres utvikling. Den eldste kjente flåteovnen er i Kerspetal (Bergisches Land). Den er datert til året 1275. I Siegerland var det rundt 30 masovner rundt 1450. Med den økende effektiviteten til ovnene og den økende etterspørselen etter maskinvare, oppsto det imidlertid et nytt problem: Kullet som kreves for energiproduksjon, kunne ikke lenger oppfylles. Kull ble forsøksvis også brukes, men kunne nesten bare av Kohlengräberei i dagbrudd vinnes. I 1755 var det nesten 200 gruver i Ruhr-området .
Engelskmannen Abraham Darby I (1676–1717) lyktes endelig i 1709 i Coalbrookdale med produksjon av grisejern ved hjelp av koks , etter at det tidligere hadde vært noen mislykkede forsøk med stenkull. Sammen med dampmotoren som ble forbedret av James Watt som drivkraft for viften, kunne effektiviteten til masovnene økes betraktelig. I Tyskland mislyktes imidlertid opprinnelige lignende forsøk først. Først i november 1796 lyktes det kongelige jernverket i Gleiwitz å bygge en funksjonell koksdrevet masovn. Ved hjelp av koks kunne mengden produsert varmt metall økes til to tonn per dag, med et forbruk på tre og et halvt tonn koks per tonn varmt metall. De fortsatt små friske ovnene kunne bare delvis behandle denne mengden råjern ; resten ble brukt som støpejern .
Med utviklingen av kupoler mot slutten av 1700-tallet opplevde støpejernindustrien en virkelig storhetstid. Kanoner , kirkeklokker , kokekar og til slutt kunstgjenstander som komfyr og ildrygger dekorert med relieffer og til og med smykker var laget av støpejern. Blant de største støpejernsproduktene er Iron Bridge i England , bygget i 1777/79, og den 12 meter lange broen over Striegau-vannet nær Laasan (nå Łażany ) i det som nå er Polen.
En endelig signifikant forbedring i ytelsen til masovner som ble stilt spørsmål ved bruken, er varm luft, som senere ble den som fremdeles ble brukt i utgangspunktet av rørovnene (Neilson, 1828) og Cowper - eksplosjonsovnen ble levert (1857).
De tidligste kjente masovnene i Europa var i Sverige på 1200-tallet, for eksempel i Lapphyttan . Individuelle masovner i Frankrike, Belgia og fremfor alt England har blitt dokumentert i de neste århundrene. Det eldste, stort sett fullstendig bevarte høyovnsanlegget i Tyskland, er Luisenhütte i Wocklum nær Balve i Sauerland . I Sachsen er det bevart tre kullovner fra 1600- og 1800-tallet i Brausenstein (1693), Schmalzgrube (1819) og Morgenröthe (1822). En masovn fra 1783 kan sees på Wilhelmshütte i Bornum am Harz og i Sauerland er Wendener Hütte, også bygget på 1700-tallet, blitt erklært et teknisk kulturminne. I Thüringen , i Schmalkalden - Weidebrunn, er det nye masovnsmuseet Neue Hütte (Schmalkalden) . Den senklassiske masovnen fra 1835 viser hvordan råjern ble produsert av lokale jernmalmer på kullbasis. Jernverket eksisterte til 1924.
Jernsmelting utenfor Europa
Tatara-ovnen , en spesiell type racingovn som brukes i Japan til å lage jern, har vært kjent siden det 7. århundre . I motsetning til ovnene som brukes i andre regioner i verden, er en Tatara-ovn bokseaktig i form med en høyde på ca. 1,2 til 2 meter med en øvre bredde på 0,8 til 1,2 meter, som strekker seg ned til bare avsmalnende ca. 0,5 meter . Ovnens lengde er derimot omtrent 4,5 meter. På begge langsider sørger 18 til 20 keramiske dyser for tilstrekkelig luftforsyning, som i "moderne" virksomheter blir hentet inn via en vifteblåser drevet av flere menn. Tataraovnen er vekselvis fylt med kull og jernmalmsand og når temperaturer på 1200 til 1500 ° C. Etter omtrent tre dager knuses ovnsveggene, og en blokk med formbart jern og stål som veier omtrent to tonn blir fjernet. Den resulterende slaggen ble tidligere drenert under drift. Selv i dag brukes japansk stål ( tamahagane ) , som tradisjonelt produseres i Tatara-ovner og kjent for sin kvalitet, for eksempel til høykvalitets kjøkkenkniver ( Hōchō ) eller til det japanske lange sverdet katana .
Kinesiske ovner for smelting av jern på 1800-tallet lignet en opp-ned avkuttet kjegle som var omtrent 2,5 meter høy med en øvre diameter på 1,2 meter, en nedre diameter på nesten 60 centimeter og en veggtykkelse på 30 centimeter og var laget av leire . For å beskytte var ovnen omgitt av en kurv laget av jernnett og kunne vippes ca. 30 ° for å gjøre det lettere å fjerne grisejernet. Brown jern sten , kull jern stein ( “Blackband”) og, avhengig av type av konstruksjon, trekull eller koks ble belastet. Luften som var nødvendig for å redusere malmen, ble hentet inn med en hånddrevet sylinderblåsere . På denne måten kunne det produseres mellom 450 og 650 kilo råjern per dag med et koksforbruk på 100 kilo per 100 kilo jern. Et lignende masovneanlegg ble også funnet i Bulacan- provinsen på Filippinene , som ble drevet til rundt 1900. Masovnen hadde form av en opp-ned-avkortet kjegle med en ytre høyde på 2,1 meter, en utvendig diameter på toppen av 1,5 meter og en veggtykkelse mellom 30 og 80 centimeter.
På begynnelsen av 1900-tallet ble det oppdaget folk i Afrika som reduserte jernmalm ved hjelp av en til tre meter høy skaft- eller trekkovner. For konstruksjonen ble det brukt termitthauger, som var passende uthulet, eller ovnen var laget av leire. Flere keramiske dyser installert i den nedre enden av ovnen sørget for tilstrekkelig tilførsel av luft, som ble sugd oppover gjennom malm- og kullfyllingen på grunn av skorsteinseffekten til den høye sjakten. Malm og kull ble etterfylt flere ganger gjennom den øvre skorsteinsåpningen, til etter omtrent 20 timer ble det laget en fille i størrelse med fotball , som ble fjernet nedenfra gjennom det ødelagte ovnsbrystet. Den veldig rene jernmalmen som kreves for disse ovnene, kom blant annet fra Banjéli i Bassariland .
konstruksjon

Komponenter fra venstre til høyre: Bunker, vinsjhus, ovngassledninger med støvpose bak skråheisen for lading, masovn, tappehall, vindvarmer
For å garantere jevn kontinuerlig drift under den såkalte " ovnen " på 10 til 20 år frem til neste vedlikeholdsdato , krever et masovnssystem andre viktige fasiliteter i tillegg til selve masovnen. Dette inkluderer bunkeren for inngangsmaterialene med et tilkoblet transportsystem for kontinuerlig mating av masovnen, med hvilken inngangsmaterialene fylles i ovnen via toppluken . Luften , som er forvarmet i varmeapparatet, blåses inn i masovnen via dyser via et varmvindrør , som er fôret med brannsikker innside og omgitt av et komplekst kjølesystem på utsiden . Koblet til masovnen er en spesialutviklet tapp- eller støpehall , der det fjernede svinejernet kan mates inn i passende øse- eller torpedovogner under den vanlige tappingen og transporteres bort for videre bearbeiding.
Byggingen av et moderne masovneanlegg er et omfattende storprosjekt av et stålverk og tar mellom 1,5 og 2,5 år fra planlegging til igangkjøring, hvorav planarbeidet tar omtrent halvparten av tiden. Investeringskostnadene for byggingen av den nye "Blast Furnace 8" i Duisburg-Hamborn, for eksempel, beløp seg til rundt 250 millioner euro.
bunker
Inngangsmaterialene, som jernmalm, koks og tilslag (f.eks. Kalk , sand og dolomitt ), som vanligvis leveres med jernbane eller skip, føres først til en bunker. Denne består av flere bunkere , som enten er muret eller støpt av armert betong og hvor innkommende råvarer lagres. For å kompensere for forskjellene i kvalitet i sammensetningen av Möller (jernmalm, tilslag) og koks, blandes materialene ofte på forhånd på såkalte blandesenger .
Noen råvarer er allerede tilberedt av leverandørene (inkludert gruver ). I noen tilfeller må et preparat oppstrøms, for eksempel i et malmknusing-, sintrings- og pelleteringsanlegg , sørge for prosessering, siden partikkel- eller kornstørrelsen på råvarene verken må være for liten (risiko for tilstopping, dårlig gassstrøm) eller for stor (ingen optimal råstoffutnyttelse).
mate
Möller og koks transporteres fra bunkeren til den øvre enden av sjakten, den såkalte gikt . Tilførselen av materialet blir også referert til som lasting eller lading og avhenger av tilgjengelig plass, enten via transportbånd , dumpebøtter eller små bulkvogner , såkalte vogntog eller hunte (også hunder ).
Ved vognlasting eller "hopp over lasting" foregår lasting via en skrå heis opp til fyllingsåpningen kalt "toppluke", som danner den øvre enden av masovnen. To heisesystemer brukes til hver masovn, som vekselvis transporterer koks og Möller. I tillegg til den større forsyningskapasiteten, fungerer bruken av to heiser også for å beskytte mot feil for å garantere uavbrutt tilførsel av masovnen. I moderne masovner er transportbånd nå foretrukket for lading. Selv om disse bare kan overvinne små stigninger og krever mer plass, er de mer effektive, lettere å automatisere og håndtere bulkmaterialet mer forsiktig.
Gikt okklusjon
Ovngassen som kommer ut ved ovnshodet består i stor grad av varmt nitrogen (N 2 ), karbonmonoksid (CO) og karbondioksid (CO 2 ) samt små mengder andre gasser og medført støv (se også under masovneprodukter ) . Til tross for farligheten med denne giftige og brennbare gassblandingen, forble giktåpningen ulåst i lang tid. Først siden utviklingen av gassovnen til masovnen på 1800-tallet ble det lagt til et låsesystem som gjorde det mulig å lade masovnen uten å miste drivstoff og varmegass som nå var blitt verdifull. Ovngassen blir fanget opp via store rør, frigjort fra støvet og deretter matet til kjelens brennere , blant annet .
Den første giktforseglingen med en enkel traktelås ble oppfunnet av George Parry i 1850 i Ebbw Vale , som senere ble kjent som "Parry-trakt". Den mest utbredte formen for toppluke-slusen frem til 1970-tallet var imidlertid den "doble bjellelåsen" med en roterende trakt utviklet av McKee og satt inn for å distribuere bulkmaterialet. Imidlertid ble systemer med tre eller fire bjeller også brukt til å redusere dumphøyden, noe som kan true den definerte diameteren på malmpellets , og når det gjelder masovner med høyere mottrykk, toppingen. Den store vekten av denne konstruksjonen og de økende problemene med å opprettholde tettheten i klokkesystemet satte endelig en begrensning på arbeidet med å øke ytelsen til masovner med klokkelåser.
Oppfinnelsen av det luxembourgske selskapet Paul Wurth SA, nemlig Édouard Legille , som i 1970/1971 utviklet den såkalte "bell-free gout seal" (senere også "Paul Wurth gout seal") medførte en betydelig forbedring i giktforseglingen . I stedet for et komplekst og tungt klokkesystem, avhengig av størrelse og krav til masovnen, er det nå to eller flere lagringstanker for koks og Möller på ovnshodet, som er fylt med bulkvogner via beltedistributører eller heisanlegg. Cola og Möller passerer gjennom nedløpsrør midt i ovnlukningen til en roterbar og svingbar renner som kan distribuere det innkommende materialet presist og jevnt på hellingsflaten. Systemet er forseglet med tetningsklaffer som er plassert over og under lagringsbeholderne. En ekstra materialklaff under beholderne sørger for konstant utladningshastighet for bulkmaterialet. Totalhøyden til den nye "klokkeløse giktforseglingen" ble redusert med rundt 1/3, noe som også reduserte konstruksjonens vekt tilsvarende, og tettheten i systemet var lettere å sikre.
9. januar 1972 ble verdens første klokkløse toppluke satt i drift på masovnen 4 i August Thyssen jernverk i Hamborn . På grunn av de mange fordelene i forhold til det gamle systemet, etablerte den klokkløse Paul Wurth giktproppen seg vellykket og er foretrukket for bruk i moderne masovnssystemer.
Masovn
design
Ovnen i seg selv ligner et sjaktovnsprinsipp , en peis eller skorstein , da disse danner grunnlaget for den resulterende skorsteinseffekten som letter optimal gassing av fôret. Høyden på masovnens kjerne bestemmer ytelsen og kan være mellom 30 og 75 m. Den øvre 3/5 danner selve akselen, som tilsvarer en langstrakt avkortet kjegle. Dette etterfølges av en kort sylindrisk mellomring med den største innvendige diameteren på masovnen, som er kjent som "kullsekken". En annen opp-ned avkortet kjegle, den såkalte "Rast", ender til slutt i den nedre, sylindrisk utformede "rammen". Kullsekk og Rast samt ramme utgjør hver 1/5 av total høyde. Med en total høyde på 30 m er sjakten ca 18 m, kullsekken og Rast ca 6 m og rammen også 6 m.
Hele masovnekonstruksjonen er vanligvis omgitt av en stålramme med arbeids- og monteringsplattformer, som på den ene siden tjener til å imøtekomme tilleggsutstyret som materialheisen og om nødvendig toppluken, men kan også brukes til å støtte og stabilisere masovnen. Det kan skilles mellom to typer støttestruktur:
Eldre og overveiende amerikanske høyovner er utstyrt med en støttering med støttesøyler omtrent på resten av nivået, hvorfra lasten som ligger på masovnen fra ovnhodet og toppluke-slusen føres inn i fundamentet. Bærekolonnene resulterer imidlertid i en innsnevring og dermed en hindring av tilgangen til tappområdet samt problemer i forbindelsesområdet mellom sperren og støtteringen. På grunn av disse ulempene er den andre varianten nå foretrukket for nyere masovner.
Dette designet, utviklet i Tyskland, er en såkalt "frittstående masovn". Stålpansringen av masovnen skaper en selvbærende ovnstruktur, som er omgitt av komplett stillas for arbeidsplattformer og for å imøtekomme tilleggsutstyret. Dette betyr at det ikke er irriterende søyler i tappområdet, og masovnen kan fritt følge alle termiske utvidelser som en kompensator festet til ovnhodet absorberer.
Den totale høyden på et slikt anlegg er rundt 90 m. Masovnen 2 i Duisburg-Schwelgern har for eksempel en ovnhøyde på nesten 75 m, en rammediameter på 14,9 m og et brukbart volum på rundt 4800 m³, smelter rundt 12 000 t råjern per dag og er for tiden i kraft (fra og med 2014) som den største masovnen i Europa. Tolv masovner i verden overstiger 5500 m³ brukbart volum (fra 2013). Den hittil største kjente masovnen til dags dato med et brukbart volum på 6000 m³ ligger i " Gwangyang Steel Works" i POSCO i den sørkoreanske provinsen Jeollanam-do.
Tappeåpningen for grisejernet, lukket med en keramisk stopper, er plassert i den nedre enden av sperren, gjennom hvilken de resulterende metallurgiske produktene jern og slagg kan dreneres. For fullstendig tømning ( "Sauabstich") i tilfelle av en kommende omforing av masovnen, en "Sauloch" (også ovn sow er) som er festet til det laveste punkt av rammen, så vel som i sin bunn .
Dysene til varmvindringslinjen starter ved grensen mellom resten og rammen og leveres av varmluftsvarmere.
![]() |
Region og periode | Ramme Ø d i m |
Høyde H i m |
Brukbart volum i m³ |
Effekt i tonn per dag |
---|---|---|---|---|---|
1) masovn 1861 | 0,9 | 15.3 | 64 | 25 | |
2) Vesttyske spesialgriseovner fra 1930-tallet | 4.5 | 20.0 | 425 | 450 | |
3) Vesttyske stål- og griseovner fra Thomas 1961 | 6.5 | 24.0 | 900 | 1200 | |
4) Vesttyske masovner 1959 | 9.0 | 26.1 | 1.424 | > 2000 | |
5) Sovjetiske masovner 1960 | 9.8 | 29.4 | 1.763 | 4000 | |
6) Japanske masovner 1968 | 11.2 | 31.5 | 2.255 | 6000 | |
7) Vesttyske store masovner 1971/72 | 14.0 | 36,7 | 4.100 | ≈ 10.000 |
Mursteinfôr
Opprinnelig besto masovner av et meter tykt, bærende og varmeisolerende mur laget av murstein eller murstein (røykvegger) og hadde et ildfast fôr på innsiden (kjernevegger) . I moderne masovner tar centimeter tykk stålrustning og bærestruktur belastningen, mens kjernemuren alene gir den nødvendige brannmotstanden og varmeisolasjonen.
For å oppnå ønsket levetid (ovnens bevegelse) til fullstendig fornyelse av ovnsforingen skyldes, er hele ovnkjernen fra skaftet til rammen ildfast . Ovnens foring definerer også den endelige indre profilen til ovnen. Med et samlet areal på rundt 2000 m² og en tykkelse på noen få desimeter til over en meter, kan overdimensjonert murverk føre til enorme kostnader, og det er derfor, selv i planleggingsfasen, blir det forsøkt å bare bruke steiner som er spesielt skreddersydd til kravene i den respektive ovnseksjonen.
I det øvre området av sjakten er temperaturene relativt lave, men de mekaniske påkjenningene er høye på grunn av belastningen av belastningen. Følgelig brukes kamoter med et korundinnhold mellom 30 og 40% her. I tillegg er "slagpanser" laget av stålplater festet i fôrområdet for å forhindre skade på murverket forårsaket av støt av mørtelmaterialene.
I det nedre sjaktområdet opp til kullsekken øker temperaturene raskt. Spenningen forårsaket av slitasje faller imidlertid bare sakte, siden belastningen skal være fast så lenge som mulig og tåle trykket fra Möll-kolonnen for å muliggjøre en god gassstrøm. I tillegg må steinene i dette området være kjemisk stabile, ettersom reaktiviteten til de omkringliggende stoffene øker. Følgelig brukes her meget ildfaste kamotter med et korundinnhold mellom 60 og 86% eller semi-grafittstein.
På nivået av tuyeres og fangstområdet som er utsatt for de høyeste temperaturene og trykket blir utsatt, som bare karbonstein , Schmelzspinellsteine med krom eller Chromkorundstein tåler.
kjøling
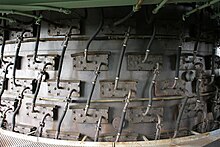
For å beskytte mot overoppheting inneholder masovnen et system med kjølevannsledninger og -elementer (stenger) som er koblet til rustningen, fra omtrent den øvre tredjedel av skaftet til bunnen av rammen . Siden en masovn med en rammediameter på 8 m har en vannomsetning på mer enn 30 000 m³ per dag, som omtrent tilsvarer forbruket i en mellomstor by med rundt 200 000 innbyggere, må kjølesystemet utformes deretter og sikres flere ganger for å beskytte mot feil.
I moderne masovner fra det 20. århundre brukes de tidligere utbredte, åpne kjølekretsene for det meste bare til vanning av ovnshode og stativ og i nødstilfeller (f.eks. Hvis en lukket krets mislykkes). I åpne kretsløp tas det nødvendige vannet fra de nærliggende vannmassene (elver, innsjøer) og renses for faste stoffer før det brukes i kjølesystemet. Etter bruk, kjøletårn overta den gjen kjøling av vannet før det føres tilbake til omgivelsene. Lukkede kretser bruker derimot behandlet, avsaltet og avgasset vann, som etter bruk via en varmeveksler blir avkjølt igjen og deretter føres tilbake til kjølesystemet. I tillegg til å beskytte kjøleelementene og ledningene mot avleiringer, har behandlet vann den fordelen at kjølesystemet kan absorbere større mengder varme.
Utformingen av kjøleelementene er utformet på en slik måte at de på den ene siden kan støtte murverket, men på den andre siden kan de også raskt byttes ut hvis de blir skadet. De består av stålplate, støpejern eller kobber og er enten skrudd, kilet eller sveiset til rustningen. Når det gjelder utformingen av kjøleelementene, kan man skille mellom to grunntyper:
- Kjølebokser er flate, rektangulære elementer med føringsplater trukket inn som en labyrint for å lede vannstrømmen og en profil som smalner mot midten av ovnen, noe som muliggjør rask fjerning og installasjon. Kjøleboksene settes inn mellom skaftets rustningsplater, slik at det opprettes et rutemønster av panserplater og kjølebokser.
- Plate kjølere eller stenger er laget av spesiell støpt med støpte, vertikale kjølerør. De skrus fast på siden av rustningen som vender bort fra midten av ovnen. Bæreflaten på stavene krysses med spor som er fylt med isolerende forbindelse.
Ulike typer kjøling brukes på masovnen, avhengig av kravene til kjølekapasitet. Ovnhodet blir avkjølt i området for støtpansringen med et eksternt sprinklersystem. For det meste er kjølebokser installert i sjaktområdet, og kjølebokser og platekjølere brukes i området Kohlsack og Rast. På grunn av den spesielt høye varmebelastningen i dette området, plasseres kjøleelementene med tette intervaller slik at mest mulig varme kan spres. Blåseformene har sin egen doble kjølekrets. Rammen og basen blir enten avkjølt med vedlikeholdsvann eller ved å introdusere vann i en dobbel rammejakke.
Varm eksplosjonsovn
James Beaumont Neilson var en av de første til å sprenge ovner i rekuperativ design - luften som kreves av varmeveksleren oppvarmet - utviklet og patentert venstre. Tidligere ble masovner alltid drevet med kald luft, ettersom metallurgiindustrien for lengst hadde opplevd at en masovn gikk bedre om vinteren enn om sommeren. Derfor møtte Neilsen opprinnelig stor motstand når han forsøkte å bruke det nye prinsippet. Arbeiderne var ennå ikke overbevist av et eksperiment med en blåservind, tillatt av Clyde Iron Works i 1828 , som bare ble oppvarmet til 27 ° C og likevel sørget for at produsert slagg var mindre jern og betydelig mer flytende. Neilsons ganske enkelt konstruerte kjele besto av et stykke hvelvformet bøyd forsyningsledning, som ble oppvarmet over en ristbrann . En metallkasse montert over rørhvelvet holdt varmen inne en stund for å forbedre varmeoverføringen. Ytterligere konstruktive forbedringer ved bruk av mer varmebestandige rør og bokser av støpejern, samt langstrakte og buede varmebatterier for å absorbere den termiske ekspansjonen, gjorde at disse "rørformede vindvarmerne" kunne varme opp blåservinden opp til 315 ° C.
år | Vindsystem | Drivstofforbruk i kg per t råjern |
Mengde råjern på 24 timer i kg |
1829 | Kald vind | Koks 8060 | 1607 |
1830 | Varm vind | Koks 5160 | 2353 |
1833 | Varm vind | Rå kull 2280 | 3556 |
Motstanden mot bruk av varm eksplosjon avtok helt etter hvert som fortjenesten til råjernet økte mer og mer, og samtidig kunne mengden drivstoff som kreves reduseres betydelig. Selv rå kull kunne nå brukes, noe som tidligere var umulig.
Masovnsgass har også blitt brukt i metallurgi siden midten av 1700-tallet, men i utgangspunktet bare for steking av malm, tørking av støpeformer og brenning av kalk og murstein. Det var ikke før Wilhelm von Faber du Faur lyktes med å utvikle en effektiv og stabil rørvarmer, "Wasseralfinger Winderhitzer", som ble oppvarmet med masovnsgass og hevet vindtemperaturen til 540 ° C. Dette betydde imidlertid også at ytelsesgrensen for dette designet ble nådd.
En avgjørende forbedring i tilførselen av masovner med varm eksplosjon ble endelig oppnådd av Edward Alfred Cowper (1819–1893) ved ikke lenger å bygge eksplosjonsvarmeren fra et rørsystem, men med ildfaste, luftgjennomtrengelige flerperforerte murstein . I den første utviklingsfasen brakte "Cowper vindvarmere" 29 m³ luft til en temperatur på 650 til 700 ° C i løpet av ett minutt. På den tiden kunne vindtemperaturen bare måles med smelteprøver av forskjellige metaller. De tidligere brukte prøvene laget av bly ( SP = 327,4 ° C) og sink (SP = 419,5 ° C) kunne ikke lenger brukes i Cowpers vindvarmere og til og med antimon (SP = 630,6 ° C) smeltet i løpet av sekunder. En annen innovasjon, også utviklet av Cowper, var den regenererende vekslende driften av to vindvarmere, der den ene ble oppvarmet ved ovngassfyring, mens den andre avga den lagrede varmen til den kalde luften som ble blåst inn.
Mer moderne “Cowper-Windheater” består av et loddrett stålrør 20 til 35 m høyt med en diameter på 6 til 9 m. Inne er det først et lag med varmeisolerende murstein og deretter et lag med ildfast murstein. Kjernen består utelukkende av stablede flerhulls silikat murstein . På den ene siden av skaftet er en brannsikker foret brenneaksel delt opp til kuppelnivået, som tar omtrent en tredjedel av tverrsnittet til varmeren. Brennerdysene og tilkoblingene for kald luft og varm luft er plassert på den nedre skyveakselen. En annen mulighet er konstruksjonen av en forbrenningsaksel som er plassert på utsiden, uavhengig av varmeakselen. Denne konstruksjonen har fordelen at det på den ene siden sprekker som oppstår i skilleveggen mellom forbrennings- og varmeakslene på grunn av de sterke temperatursvingningene unngås, og på den annen side har selve varmeren mer plass til flerperforert steiner og dermed kan varmeeffekten økes igjen.
Vanligvis sørger tre, når det gjelder større masovner, også fire “cowperser” for en jevn og problemfri tilførsel av varm luft til masovnen. Mens to varmes opp til forskjellige tider, skyver en aksial eller radiell vifte kald luft (rundt 1,4 t per tonn svinejern) gjennom den tredje varmeapparatet ved et trykk på 2 til 4,5 bar. De tidligere brukte damp- eller gassstempelblåsere viste seg å være uøkonomiske og vanskelige å kontrollere. I en kontinuerlig syklus skjer det en endring av den tidligere oppvarmede kåpen, mens den avkjølte kappa blir varmet opp igjen. Oppvarmingsfasen tar omtrent 50 minutter, vindfasen imidlertid bare ca. 30 minutter, siden vindvarmeren ikke må falle under en temperatur på 721 ° C, noe som er kritisk for kiselsten. Under denne temperaturen gjennomgår kiselstein flere endringer av modifikasjoner , noe som fører til et "volumhopp" som ødelegger den faste strukturen til den flerperforerte mursteinsrammen og kan føre til at den kollapser. Den tredje eller fjerde “cowparen” fungerer også som en reserve mot feil og under vedlikeholdsarbeid.
Varmvind ringlinje og dyser


Med en maksimal oppnåelig temperatur på 1270 ° C (1980) til 1350 ° C (1985) når den varme sprengningen "hot blast ring line" til de mellom 10 og 40 dysene, avhengig av størrelsen på masovnen, og via de såkalte blåseformene inn i ovnen. For å redusere forbruket av koks blåses erstatningsreduserende midler som animalsk fett eller tung fyringsolje i formene i mange planter. Men siden oljeprisen fortsatte å stige over tid, var det forskjellige forsøk med andre erstatninger.
I Armco i USA ble kullstøv vellykket brukt som drivstofferstatning i lengre perioder og i kinesiske selskaper fra 1963 og utover. Siden 2006 har det også blitt tilsatt finpellert gammel plast (6 mm × 9 mm), som i tillegg til miljøvennlig gjenvinning av plastavfall , i motsetning til deponi, også reduserer utslipp av CO 2 og SO 2 .
For å beskytte mot skade forårsaket av varmebelastningen, får ringledningen og forsyningstilkoblingen et brannsikkert fôr, som også har en varmeisolerende effekt for å unngå varmetap. Blåseformene selv blir avkjølt intensivt med vann fordi de, avhengig av graden av slitasje på ovnsforingen, kan stikke opp til en halv meter inn i ovnen og deretter utsettes for de høyeste belastningene på grunn av temperaturen og trykket på kolonnen Möll. I moderne masovner brukes derfor bare hule former laget av elektrolytisk kobber med dobbeltkammer kjølevannskrets. Hvis frontkammeret brenner ned under ovnen, kan den aktuelle kjølekretsen slås av, og hovedkammeret kan fortsette å gå til neste stillstand.
Tapp av jern og slagg

Den råjern - reoler med jevne mellomrom på ca to til tre timer. Her, den keramiske plugg ved tappehullet er med en komprimert luft - drill bores. I sjeldne tilfeller, for eksempel hvis boret svikter, er åpningen gjennomboret med en oksygenlanse .
Grisejernet flyter deretter i rundt 15 til 20 minutter i en spesialutviklet hane- eller støpehall med en arbeidsplattform og et brannsikkert murkanalsystem, som i tillegg er stemplet eller hellet med ildfaste forbindelser. I eldre masovner med høyere slaggproduksjon ble en del av slaggen først tappet av som såkalt "pre- slagg " på nivået av formplattformen. Deretter ble grisejernet og slaggen tappet sammen ved hjelp av en slags sifon, den såkalte " reven ", som separerte slaggen fra grisejernet (som dekantering ) og avledet den i forskjellige retninger via et tilsvarende designet kanalsystem. Moderne masovner med lavere slaggproduksjon, men en daglig råjerneproduksjon på 3000 tonn og mer, trenger ikke forhåndsuttak av slaggen, men mellom to og fire tapphull. Systemet med takrenner og rev er tilsvarende komplekst og krever nøye overvåking.
I hovedkanalen mellom kranhullet og reven, som er rundt 8 til 14 meter lang og har rundt 20 til 60 tonn svinejern inkludert slagg, har slaggen tid til å skille seg fra grisejernet og samle seg på overflaten. Foran reven, hvis "nese" faller ned i smelten, bygger slaggen seg opp og blir drenert av via kanaler som forgrener seg til siden. Grisejernet strømmer derimot under reven gjennom til et hull under hvilket en øse eller torpedovogn er klar til å transportere det fangede jernet til stålet eller støperiet for videre bearbeiding . Slaggen samles også i spesialvogner og transporteres bort for videre behandling.
Etter avsluttet tappefase lukkes tapphullet igjen ved hjelp av en "tappemaskin for tapphull" til neste trykk.
Moderne støpehaller må "støves av" for å beskytte ansatte og miljøet, noe som betyr at sugesystemer installeres i kranhullene og ved overføringspunktet til oppsamlingsbeholderne og kanalsystemet er dekket av stål plater. De fangede avgassene blir renset i passende filtersystemer .
funksjon
Blås videre
Før en ny masovn kan gå i produksjon, må den først tørkes sakte ved hjelp av gassbrennere eller ved å blåse inn varm luft. Først da finner den faktiske "blåseringen" inn i ovnen sted. Valget av blåsmetode har stor innvirkning på den påfølgende driftsmåten og levetiden, kan variere fra anlegg til anlegg og tar omtrent en til to uker (med eldre masovner noen ganger til og med flere måneder).
Etter tørking fylles rammen for tre og koks for første gang. I skaftet over helles lag av koks og moleren som består av jernmalm og slaggbindende tilslag, antennes og vifter ved å blåse inn varm luft. Sammensetningen av den blåste stratifiseringen er veldig forskjellig fra den senere operative stratifiseringen. Den inneholder betydelig mer koks, ettersom oppvarming av ovnsforingen og den kalde cola-Möller-kolonnen bruker mye energi. Bruken av en tilsvarende høy mengde slagg sørger for at rammen varmes opp og beskyttes.
Strukturen og oppførselen til lasten under ovnens passasje
Formen, sammensetningen og de mekaniske egenskapene til fôret, spesielt malmene, så vel som en kornstørrelse som er så jevn som mulig, er av avgjørende betydning for effektiviteten til en masovn . Reduksjonsatferden ved forhøyet temperatur spiller også en rolle, og målet er å oppnå så lav nedbrytning ved lav temperatur som mulig og en høy mykningstemperatur med et samtidig lavt temperaturområde for bløtgjøringsfasen. Bare hvis sinter og pellets forblir i stykker og i solid tilstand så lenge som mulig, kan de tåle trykkbelastningen til lagene over og garantere god gassinntrengning.
Den reduserbarheten av den sinter er avhengig av dets sammensetning, og er avhengig av empiriske størrelsen av basisitet
som viser masseforholdet av kalsiumoksyd og magnesiumoksyd til silisiumdioksyd . Reduserbarhet er bedre hvis basisitet i sammensetningen er i det grunnleggende område (B> 1,0) og når et maksimum reduserbarhet i området 2,0 til 2,5. Den mekaniske styrken er også størst i dette området. Fra en basisitet på 2,6 og høyere øker andelen av smeltefasen i den sintrede delen, som lukker porene og reduserer evnen til å redusere, siden de reduserende gassene ikke lenger når malmdelen direkte. Når det gjelder sur sintring (B <1,0), begynner mykningsfasen i noen tilfeller når bare ca. 15% av malmen er redusert.
I motsetning til sinter har pellets en sur sammensetning, fordi deres stabile sfæriske form betyr at det er mindre tendens til finkorndannelse og forverring av mekaniske egenskaper. Pellets består derfor hovedsakelig av hematitt , forskjellige silikater for å binde slagg og porer. Andelen hematitt må imidlertid forbli begrenset, siden ellers ville strukturen til pellets løsne seg for mye i løpet av reduksjonen, og pellets ville til slutt oppløse seg i konsentrert støv, noe som ville resultere i et betydelig tap av trykkfasthet. Samtidig overdreven økning i pelletsvolumet (terskler) har også risikoen for tilstopping av masovnen.
For å finne ut hvordan strukturen og tilstanden til lasten endres på vei fra ovnen til kranåpningen og hvilke reaksjoner som foregår i den respektive ovnseksjonen, ble det utført flere tester på 1970-tallet, hovedsakelig i Japan, hvor masovner ble stoppet midt i produksjonen og avkjølt den intenst med vann. Alle pågående reaksjoner i Möllersäule ble så og si ”frosset”. De påfølgende analysene av lagets sammensetning på forskjellige nivåer viste at myknings- og smeltesonen buler oppover i form av en bjelle på sentralaksen. Sentrum av klokken består av koks, som fortsatt er gassgjennomtrengelig i varmesonen 1000 til 1600 ° C. Smeltende malm og slagg når innsiden via denne aktive koksklokken og synker ned i hvile og ramme, mens den varme vinden som blåses inn fordeles jevnt utover og oppover. Den såkalte “døde mannen” - en statisk og ikke-responsiv, kjegleformet kropp laget av koks og stivnet jern - eksisterer ikke.
Bare foten til denne "sammenhengende sonen" er ugjennomtrengelig for gass og er ideell plassert på nivå med resten. Det skal heller ikke påvirkes av gassen, slik at på den ene siden leveringen (ildfast fôr) av kullsekken og resten blir mindre påvirket, og på den annen side vil den resulterende turbulensen til den varme vinden gjøre en jevn reduksjon av lasten vanskeligere eller til og med forhindre det. For å optimalisere gassstrømmen i den beskrevne formen og dermed redusere energiforbruket samtidig som kvaliteten på grisejernet økes, en nøye beregning av sonens tverrsnitt samt mengden og sammensetningen av det varme eksplosjon innført er av stor betydning.
Følgende ytterligere funn ble oppnådd fra undersøkelsen om "frosne" masovner:
- Den skiftende ladingen av Möller og Coke opprettholdes gjennom ovnen og løper ned til de dypere lagene. Bare lagtykkelsene blir mindre i løpet av reduksjonen.
- På nivået med blåserplanet, i stedet for fast malm, er det bare dråper metallisk jern og koks blandet med slagg.
- Reduksjonen begynner 3 til 4 meter under lastenivået, med det resultat at kornstørrelsen på sinter, pellets og klumpmalm reduseres jevnt. Sinteren brytes ned ved en temperatur på 200 til 500 ° C, mens den for klumpmalm bare forekommer ved rundt 800 til 900 ° C.
- 7 meter under overflaten har reduksjonen kommet så langt at sinterpartiet ikke brytes ned lenger. Dette gjelder imidlertid ikke den andre Möllerstoff, siden det ble funnet en stadig økende andel finkorn under 5 millimeter opp til 18 meters dyp. Hvorvidt og på hvilket tidspunkt det dannes fint korn i masovnen, avhenger av temperaturen og gassstrømningsfordelingen, oppvarmingshastigheten og ladetypen. Ved sintring er andelen finkorn generelt høyere.
- Reduksjonen er mye raskere midt i ovnens tverrsnitt enn i kantområdet.
- På giktens høyde reduseres fastheten til alle stoffer i oljen i utgangspunktet kraftig og øker igjen med økende dybde, noe som er relatert til reduksjonens progresjon og den tilhørende økningen i jerninnholdet.
Reduksjon av skadedyrs svovel
Alkalier og svovelforbindelser som alltid er tilstede i tilførselen har stor innflytelse på reduksjonsprosessene . Spesielt svovelforbindelsene har en særlig ugunstig effekt på reduksjonsprosessene som pågår, siden de aldri kan drives ut til tross for den komplekse forbehandlingen av malm og koks. Selv små mengder av svoveldioksyd (SO 2 ) fra omkring 5 til 50 ppm i den reduserende gass til å begynne å akselerere nedbrytningen av oksygen betraktelig; Men så snart det første metalliske jernet dukker opp, blir prosessen snudd og nedbrytningen av oksygen reduseres kraftig. Årsaken til denne reaksjonen er egenskapen til svovel å kombinere med det metalliske jernet på overflaten og derved forhindre absorpsjon av karbon.
Reaksjonen av wustitt (jern (II) oksid, FeO) med karbonmonoksid (CO) skjer vanligvis ikke bare over overflaten av FeO, men også over overflaten av jernet som allerede har falt ut. På grunn av den bedre absorpsjonsegenskaper av jern, en stor del av gassen transport til og fra jern-jernoksyd fasegrensen finner sted via den samme . Dette skjer imidlertid bare når jernet har kunnet absorbere (karburer) tilstrekkelig karbon. Hvis absorpsjonen av karbon blokkeres av svovelet, kan reduksjonen bare skje på overflaten av jernoksidet.
Svovelet som et reduksjonsskadedyr er også årsaken til overdreven hevelse i pellets, som beskrevet ovenfor. Siden jernet bare kan krystallisere seg i retning av det nedbrytende jernoksydet, utvikler jernkrystallene seg på en langstrakt, fibrøs måte. Pelletsstrukturen som allerede er løsnet på grunn av det første reduksjonstrinnet forsterkes igjen, og pelletsvolumet kan vokse til to til tre ganger sitt opprinnelige volum.
For å holde andelen svovelforbindelser så lave som mulig omdannes sulfidmalmer til oksider ved nøye steking og svovelbindende tilsetningsstoffer innføres.
Kjemiske reaksjoner under reduksjonen
I masovnen finner forskjellige metallurgiske prosesser noen ganger sted samtidig, der på den ene siden jernmalmen reduseres til råjern over flere trinn, og de ikke-reduserbare komponentene overføres til slaggen.
For å starte en reduksjon i jernmalm, må imidlertid de nødvendige reduserende gassene først genereres. Dette skjer i det nedre området av masovnen når karbonet som er inneholdt i koks blir brent med oksygen .
Reaksjonen er sterkt eksoterm , noe som betyr at det frigjøres varme, som er 394,4 kJ / mol i denne reaksjonen og masovnen i området med de varme sprengningsdysene til en temperatur på 1800 til 2000 ° C, med bruk ekstra oksygen til og med oppvarmet til 2200 ° C. Imidlertid senker to umiddelbart etter endotermiske , dvs. varmekrevende reaksjoner temperaturen igjen til rundt 1600 til 1800 ° C.
Den såkalte " Boudouard-reaksjonen " , som imidlertid krever en minimumstemperatur på 1000 ° C, krever 172,45 kJ / mol.
En samtidig spaltning av vanndampen i den varme gassen krever ytterligere 131,4 kJ / mol.
De to gassene som kan reduseres, karbonmonoksid og hydrogen, stiger mot strømmen av materiale i masovnen. På grunn av denne egenskapen - synkende Möller-koksøyle på den ene siden og stigende reaksjonsgasser som strømmer mot det bevegelige bulkmaterialet på den andre - blir også ovnen referert til som en "motstrømsreaktor" og en "bevegelig sengreaktor".
Den såkalte "indirekte reduksjonen" finner sted i temperaturssonen mellom 400 og 900 ° C. De forskjellige jernoksidene reagerer med karbonmonoksid eller hydrogen i tre trinn, til endelig metallisk jern er til stede:
Reaksjon med karbonmonoksid (CO) | Reaksjon med hydrogen (H 2 ) |
---|---|
Jo mer jernholdig magnetitt er dannet av hematitt . | |
Av magnetitt produsert wustite . | |
Metallisk jern er laget av wüstite og akkumuleres i masovnen nedenfor. |
Så lenge det resulterende karbondioksidet (CO 2 ) holder seg i temperaturområdet over 1000 ° C, regenereres det gjentatte ganger til karbonmonoksid (CO) ved Boudouard-reaksjonen og er tilgjengelig igjen for reduksjonsprosessen. Reduksjonen med hydrogen er spesielt effektiv ved rundt 800 ° C. Et innhold av bare 10% hydrogen i reaksjonsgassen tredobler reduksjonshastigheten, men denne avtar igjen med en ytterligere temperaturøkning. Malmens kornstørrelse må heller ikke overstige et visst nivå slik at diffusjonsveiene til hydrogenet ikke blir for store.
I temperaturområdet 900 til 1600 ° C er det også en "direkte reduksjon" med karbon:
Jernkompanjongene mangan , silisium og fosfor er også inkludert i prosessen og reduseres, hvorved varme forbrukes:
Samtidig tar det allerede reduserte jernet i karboniseringssonen opp karbon ved rundt 1100 til 1200 ° C, enten direkte fra den glødende koks eller fra karbonmonoksydgassen.
Opptaket av karbon senker smeltepunktet fra 1538 ° C (rent jern ) til rundt 1300 til 1400 ° C (smeltepunkt for den eutektiske blandingen , ledeburitten , med 4,3 vekt% C: 1147 ° C).
Overvåking og regulering av masovnsprosessen
I løpet av automatisering og kvalitetssikring for å opprettholde konkurransekraft på den ene siden, og de økte sikkerhetskravene til beskyttelse av mennesker og maskiner på den andre, er forskjellige måle- og kontrollanordninger uunngåelige. Smelteprosessen er naturlig utsatt for større eller mindre svingninger, da sammensetningen av Möller, koks og varmeksplosjon, inkludert tilsetningsstoffene som er blåst inn, også varierer innenfor toleransegrensene . Reaksjonens forløp og hastighet svinger tilsvarende, noe som uten overvåking og passende motreguleringstiltak vil føre til alvorlige forstyrrelser.
Viktige målte variabler er fremfor alt:
i mengden gikt |
|
fra sjakt til kullsekk |
|
på nivået med varmlufttilførselen |
|
på bunnen av rammen |
|
I tillegg brukes horisontale sonder også til å måle tykkelsen på Möll-lagene, så vel som trykket og hastigheten på gassen som passerer gjennom Möller-kolonnen. For å beskytte mot feil, er noen måleinstrumenter overflødige , for eksempel for å måle dybden på lasteflaten.
Forstyrrelser i masovnsprosessen
Hengende lasting
På grunn av oppløsningen av Möller og koks under reduksjonen, kan Möller-søylen i sjakten bli komprimert og til slutt sikkerhetskopiere. En Möll-søyle som henger på denne måten merkes i utgangspunktet ved at dybdemålingen ikke lenger registrerer noen synkende bevegelser på lasteflaten, men trykket og temperaturen på toppgassen faller også fordi det er vanskelig å komme gjennom de stadig smalere hullene i komprimert Möll-søyle. Vindtrykket øker derimot fordi det møter større motstand.
Under hengesonen fortsetter imidlertid reduksjons- og smelteprosessen uforminsket til det til slutt dannes et hulrom mellom den hengende og synkende Möller. Siden det på den ene siden er risikoen for at en Möller-søyle plutselig kollapser i hulrommet, fører til alvorlige prosessforstyrrelser og skade på masovnen, og på den annen side truer jern og slagg å stige til blåseformene, en reaksjon på nevnte karakteristiske endringer i måleresultatene må skje så tidlig som mulig. Dette inkluderer for eksempel den såkalte "upsetting", en engangs eller, om nødvendig, gjentatt sterk struping av vindmengden og dermed mottrykket på Möll-kolonnen, som tvinger den til å gli på grunn av sin egen vekt.
Tilnærming formasjon
Kaking av Möller og koks på masovnens indre vegger kan ha forskjellige årsaker. Over tid endres rustningsprofilen på grunn av fysisk og kjemisk slitasje , noe som kan føre til lettere festeforhold på steder. Som et resultat letter utstikkende kjøleelementer også dannelsen av avleiringer. Selve mørtelets sammensetning har også innflytelse på kappeprosessen, ettersom blant annet en basisk slagg har en tilsvarende høyere andel forskjellige baser , som fungerer som kakemiddel, for bedre svovelbinding . Mindre partier er knapt merkbare i begynnelsen, men kan vokse veldig raskt og føre til funksjonsfeil i masovnsprosessen; spesielt hvis disse plutselig bryter av og deretter forårsaker uregelmessigheter i sammensetningen av Möllersäule.
Større tilnærminger kan måles ved å begrense ovnens tverrsnitt og dermed øke vindens strømningshastighet , som medfører flere støvpartikler. I tillegg til økt støvutslipp, kan dannelsen av avleiringer også fremme de nevnte hang-ups. Videre er svingninger i ovnssyklusen og i kvaliteten på grisejernet på grunn av smuldrende avleiringer. Til slutt kan oppbygging av utstikkende kjøleelementer også skade dem.
Ved hjelp av trykk- og temperatursensorer i ovnsveggene samt måleprober som kan skyves horisontalt inn i Möll-kolonnen, kan endringer i tverrsnitt og dermed tilnærminger nå lokaliseres raskere og mer presist. Passende endringer i sengetøy kan da vanligvis eliminere disse. Tidligere måtte særlig større masovner blåses ned først, og deretter ble tilnærmingene boret eller sprengt av.
Inntrengning av vann
Inntrengning av vann gjennom ødelagte kjøleelementer kan føre til betydelige forstyrrelser i masovnsprosessen, siden fordampningsvannet med større mengder medfører et høyt tap av termisk energi og de forskjellige reduksjonsprosessene stopper. En vanninntrengning kan måles på den ene siden av et økt hydrogeninnhold i toppgassen og på den andre siden av det økte forbruket av matevann , som skal kompensere for vanntapet i lukkede kjølekretser.
Fornuftig inndeling og tilkobling av kjøleelementene og linjene med hverandre i horisontale soner eller "kjøleskiver" gjør at skadede elementer kan oppdages og erstattes raskere og vanntap holdes på et minimum. I åpne kjølesystemer er det imidlertid nødvendig med en trykktest på hvert kjøleelement.
Skru av
Ulike prosedyrer er nødvendige, avhengig av om jern- og stålverket bare vil stenge masovnen (dampende) eller slå den helt av og slå den av (blåser ut) .
Dampende
Hvis en masovn bare skal stenges midlertidig, for eksempel i tilfelle forsyningsflaskehalser eller mindre reparasjoner, dempes den . Ved å gjøre dette blir lasten først slått av, avhengig av den planlagte varigheten av driften. Den består nå på den ene siden av en "lett" dampende smører, som betyr mindre jern, og på den andre siden av et høyere antall lag med koks. Under det siste springen før stenging, er det påpasselig at grisejernet og slaggen renner av så fullstendig som mulig. Hvis dampfasen skal vare lenger, brukes også ovnssåen. Når ovnen står stille, stenges alle tilførsels- og utløpsledninger, varmluftdysene blir muret opp og ladeoverflaten dekkes med fin malm eller slaggesand, slik at ovnen kan beholde varmen så lenge som mulig og naturlig trekk fører ikke til unødvendige koksforbrenninger. For å forhindre vanninntrenging, noe som vil føre til alvorlige forstyrrelser i masovnsprosessen, blir kjølesystemet bare slått av etter en nøye lekkasjetest.
Gjenoppblåsingen etter lengre dempingsfaser utføres i omvendt rekkefølge av de enkelte arbeidstrinn under damping, selv om det i utgangspunktet bare er noen få tuyer av det varme sprengningssystemet i kranhullområdet, og deretter blir ytterligere dyser satt i drift. Om nødvendig settes nålehullet også høyere i noen tid.
Blåse ut
Hvis regelmessig drift ikke lenger er mulig, blant annet fordi foringen er så slitt at den må byttes ut, blir masovnen "blåst ut".
Masovnsprosessen fortsetter i begynnelsen i det nedre området, men matetilførselen er slått av og vindtilførselen reduseres kraftig i den innledende fasen og til slutt også slått av. I dypblåsingsfasen (senking av cola-Möller-kolonnen) injiseres vanndamp gjennom spesielle dyser på alle punkter der "døde", dvs. tomme rom dannes. Noen ganger tilsettes vann også ovenfra. Dette forhindrer dannelsen av eksplosive gass-luft-blandinger. Døde mellomrom oppstår over alt over lasteflaten opp til toppventilen, men også i mellomrommene mellom toppgasslåsen, avhengig av posisjonen til stengeventilene på gassventilen mellom ovnen og støvposen eller i støvet selve posen, så vel som i virvler og i ovnsventilen. En annen metode for å unngå gasseksplosjoner er å brenne av ovngassene som renner ut fra ladeflaten ved hjelp av en kontinuerlig brennende antennelanse for koksgass. Fullføringen av utblåsingen er tapping av ovnssøyen , hvor i tillegg til slagg, avhengig av varigheten på masovnens reise og kjøleforholdene i stativet, kan akkumuleres flere tonn svinejern.
Ved slutten av ovnen, blir hele ildfast mursteinforingen vanligvis fornyet og skadede stålkomponenter erstattet. Ofte blir en slik ovnstopp også brukt til å erstatte teknisk utdatert utstyr som måle- og analyseanordninger med nye. I tillegg til å forbedre kvaliteten på masovneproduktene, hjelper dette også med å redusere energiforbruk og miljøforurensning.
Det tar vanligvis flere måneder før alle skadede eller utdaterte komponenter byttes ut. Imidlertid, hvis de gjenværende komponentene er av god kvalitet, kan en masovn overleve flere ovnsreiser til den til slutt blir stengt. I mars 2008 startet for eksempel “Large Blast Furnace 1” i Duisburg-Schwelgern sin femte ovntur.
Høstovnsprodukter
Råjern
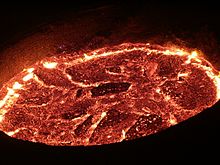

Målet med en optimalt justert masovneprosess er produksjon av høyeste kvalitet svinejern som har så lite fremmedlegemer som mulig og ikke har absorbert for mye karbon.
I henhold til DIN EN 10001 er grisejern definert som en legering laget av jern med mer enn 2% karbon og noen andre elementer med følgende maksimale proporsjoner: mangan ≤ 30%, silisium ≤ 8%, fosfor ≤ 3% og krom ≤ 10 %. Andelen andre tilsetninger bør ikke overstige 10%. For kvalitetssikringsformål tas en prøve for en kjemisk analyse ved hver tapping.
Såkalte “white råjern” (også stål råjern ) er produsert i 9 av 10 Masovn planter, i hvilke Karbonet er bundet i form av jernkarbid eller mangan karbid og bruddflaten har en lys, sølv -hvit glans . Hvitt jern er vanligvis direkte i flytende form ved bruk av lukkede torpedobiler til nærliggende stål som transporteres, men kan også lagre enten praktiske ingots eller jernkorn (kornstørrelse ≈ 2-16 mm). Hvitt grisejern brukes som utgangsmateriale for stålproduksjon og frigjøres fra dets uønskede ledsagende stoffer og en stor del av karbonet i en stålstålfabrikk ("stålkjele") ved å blåse inn oksygen. Disse etterlater det glødende, ferdige stål enten som gasser (svoveldioksid, karbondioksid) eller med tilsetningsstoffene som slagg (kalsium- og mangansilikater eller fosfater).
Den lille resten av jernverket produserer for det meste "grå grisejern" (også støperij ), hvor karbonet krystalliserer ubundet som grafitt og bruddoverflaten viser en mørkere matt grå. Grått grisejern brukes som råmateriale for produksjon av forskjellige typer støpejern, for eksempel grå støpejern med lamellær grafitt eller sfæroid grafitt , formbart støpejern og støpejern . Noen få selskaper har også spesialisert seg på spesielle typer råjern , som ferromangan (stekt jern) eller jernkisel .
slagg
Det produserte under masovn prosessen slagg som består av omtrent 38-41% kalsiumoksyd (CaO), 7-10% magnesiumoksyd (MgO), 34-36% silisiumdioksyd (SiO 2 ), 10-12% aluminiumoksyd (Al 2 O 3 ), 1, 0-1,5% svovel (S), 1,0% titandioksid (TiO 2 ), 0,16-0,2% jernoksid ( FeO ) og forskjellige andre oksider og sulfider.
Erfarne smelteverk kan ofte se den fortsatt flytende slaggen for å se hva dens omtrentlige sammensetning og egenskaper er. En enkel “kroktest”, der en jernkrok dyppes i slaggen, er vanligvis tilstrekkelig for å teste det samme. Hvis slaggen forblir på kroken i korte, tøffe dråper når den løftes (kort slagg) , er den " grunnleggende " med et vektforhold på CaO: SiO 2 > 1,0. Hvis derimot slaggen løper av kroken i lange tråder (lang slagge) , er den "sur" med forholdet CaO: SiO 2 <1,0.
Mens slaggen i masovnen fortsatt hadde til oppgave å absorbere den gangart av de malmer og asken av koks, avsvovling av råjern, og som tjener som en beskyttende vegg i rammen mot varmestråling, etter å ha trykket, avhengig av dets sammensetning og egenskaper blir det et verdifullt råstoff for forskjellige formål fortsatte å bli brukt. I tillegg til genererende masovn-slagg , slagg murstein eller -bims og slaggull er det også vei og jernbaneballast , slagg blokker , Portland-sement og masovn sement behandlet.
Ovngass

Toppgassen som kommer ut av toppen av masovnen ved en temperatur på 150 til 200 ° C består av 22-24% karbondioksid (CO 2 ), 18-21% karbonmonoksid (CO), 52-59% nitrogen (N 2 ), 1-3% hydrogen (H 2 ) så vel som fra vanndamp og spor av metan . I tillegg til sin viktigste anvendelse som et drivstoff leverandør for avfyring av vind ovner, er det også brukes, blant annet som oppvarme gass i valsemøller , dampkjeler , forkoksningshastighet kamre og i fjernvarmesystemer så vel som brensel for gassmotorer .
På grunn av mange tiltak for bedre malm- og gassutnyttelse samtidig som koksforbruket reduseres, falt den totale mengden produsert masovnsgass så vel som brennverdien over tid. Siden 1990-tallet er det produsert omtrent 1500 til 2000 m³ ovngass med en brennverdi mellom 3150 og 3570 kJ / m³ per tonn råjern . Ved å tilsette koks eller naturgass øker denne verdien til rundt 4500 kJ / m³. I tillegg er det rundt 25 kg masovnsstøv per tonn råjern, noe som tilsvarer et støvinnhold i masovnsgassen på rundt 20–30 g / m³.
For å beskytte brennere, gassmotorer og turbiner som drives av ovnsgassen mot skade ved slitasje , men også av hensyn til miljøbeskyttelse , er ovnsgassen blitt trukket ut og rengjort siden begynnelsen av det 20. århundre . Masovnens gasturbiner siden 1970-tallet krever z. B. høyrent gass med et støvinnhold på maksimalt 0,5-1 mg / m³.
Rensingen foregår i flere trinn fra tørr grov rengjøring ved hjelp av støvposer og virvlere for våt rengjøring i gass skiver og sprengmidler til finrensing ved hjelp av pose eller posefiltersystemer og elektrostatiske filtre . Den rene gassen som deretter kan brukes, inneholder fortsatt et støvinnhold på 0,006 til 0,03 g / m³.
Ytelse og forbruk
Fram til 1914 leverte en masovn rundt 300 til 400 tonn råjern per dag, og mellom 1950 og 1960 var den allerede i stand til å produsere 2500 tonn per dag.
På 1970-tallet leverte de beste ovnene i verden 60 tonn per kvadratmeter rackoverflate og mer per dag, med et gjennomsnittlig forbruk av koks og olje på rundt 503 kilo per tonn råjern. For mellomstore masovner med en rammediameter på 10 til 11 meter tilsvarer dette en daglig produksjon på 5000 til 6000 tonn.
I 1980 var det spesifikke koksforbruket til en masovn i Forbundsrepublikken Tyskland rundt 515 kilo per tonn råjern. Det spesifikke forbruket av fyringsolje var 23 kilo per tonn råjern. I 1994 hadde koksforbruket sunket til rundt 379 kilo, mens fyringsoljeforbruket steg til rundt 45 kilo per tonn. Siden 1985 har kull i økende grad blitt brukt som reduksjonsmiddel i stedet for bearbeidet koks.
Store høyovner som "Blast Furnace 5" av Rogesa- masovnen på fabrikklokalene Dillinger Hütte med en rammediameter på 12 meter produserer rundt 7.000 tonn per dag. Større masovner kan produsere opptil 12.000 tonn råjern per dag.
I 1950 var den årlige globale produksjonen på rundt 189 millioner tonn råjern, men økte til rundt 1808 millioner tonn innen utgangen av 2018. ThyssenKrupp Steel's "Blast Furnace 2" i Schwelgern , som startet opp i slutten av 1993 , hadde en rammediameter på 14,9 meter og en daglig produksjon på mer enn 10 000 tonn råjern.
I 2007 produserte store masovner med en rammediameter på rundt 15 meter i gjennomsnitt rundt 12 000 tonn råjern per dag, noe som tilsvarer en årlig produksjon på rundt 4 millioner tonn. For å oppnå dette kreves det rundt 19 200 tonn jernmalm, 4000 tonn koks, 1750 tonn injisert kull (kullstøv som skal injiseres gjennom varmluftdysene) og 11 millioner kubikkmeter luft hver dag. Dette tilsvarer et forbruk på rundt 1600 kilo malm, 330 kilo koks, 146 kilo injisert kull og 917 kubikkmeter luft per tonn råjern. Biproduktene produserte 3300 tonn slagg og 17 millioner kubikkmeter ovngass per dag. Cirka ett tonn koks brukes til å smelte slaggen for hvert 3,2 tonn slagg.
Se også
Kilder og referanser
litteratur
Direkte kjøp av masovnen
- Manfred Rasch (red.): Koksovnen fra 1709 til i dag. 2. utgave. Klartext Verlag , Essen 2015.
- Hans Schoppa: Hva masovnsoperatøren trenger å vite om sitt arbeid . 4. utgave. Verlag Stahleisen, Düsseldorf 1992, ISBN 3-514-00443-9 .
- Gerhard Winzer, Eberhard Reichenstein: Utvikling av masovnsteknologi . Rapporter holdt i kontaktstudien “Metallurgy of Iron; Del I: Strykejern ”. I: F. Oeters, R. Steffen (red.): Metallurgie . teip 2 . Verlag Stahleisen, Düsseldorf 1982, ISBN 3-514-00260-6 , s. 79-84 .
- H. Dickmann: Utvikling av oppvarming av masovn opp til oppfinnelsen av EA Cowpers . I: Brohltal AG for stein- og leireindustri (red.): Hundre år med Cowper vindoppvarming . Burgbrohl (distrikt Koblenz) 1958.
- MA Pavlov (М. А. Павлов): Design og beregning av masovner . I: Metallurgi av råjern . 2. utgave. teip 3 . VEB Verlag Technik, Berlin 1953, DNB 453723004 , lisensnummer Dg.-Nr. 370/39/53 (DDR) - (russisk: Металлургия Чугуна, Часть третья: Доменная печь . Oversatt av Erich Marquardt).
Masovn prosess
- K. Grebe: Möllers og koks masovnens oppførsel . Rapporter holdt i kontaktstudien “Metallurgy of Iron; Del I: Strykejern ”. I: F. Oeters, R. Steffen (red.): Metallurgie . teip 2 . Verlag Stahleisen, Düsseldorf 1982, ISBN 3-514-00260-6 , s. 85-145 .
- MA Pavlov (М. А. Павлов): Den masovn prosess . I: Metallurgi av råjern . 2. utgave. teip 2 . VEB Verlag Technik, Berlin 1953, DNB 367559374 , lisensnummer Dg.-Nr. 370/40/53 (GDR) - (russisk: Металлургия Чугуна, Часть вторая: Доменный Процесс . Oversatt av Rudolf Rickert, Walter Philipp, Alexander Junge, Heinz Frahn).
- Association of German Ironworkers (Red.): Masovnsprosessen - Den kinetisk-dynamiske simuleringsmodellen . Rapport om et felles arbeid med bidrag fra forelesningskonferansen "Matematiske modeller for masovnsprosessen" 2. og 3. desember 1971 i Düsseldorf. Verlag Stahleisen, Düsseldorf 1973, ISBN 3-514-00124-3 .
- Richard Troska: Ovnens dimensjoner basert på ovnprosessen . Weimar 1867 ( tilgjengelig online i Googles boksøk, sist tilgjengelig 27. mai 2012)
Generell
- Jürgen Ruge, Helmut Wohlfahrt: Materialteknologi . 8. utgave. Springer Verlag, 2007, ISBN 3-8348-0286-7 .
- Karl Taube: Stålproduksjonskompakt: Grunnleggende om jern og metallurgi . Vieweg Technik, Braunschweig / Wiesbaden 1998, ISBN 3-528-03863-2 , s. 60–159: masovn .
- Del I: Strykejern . Rapporter holdt i kontaktstudien “Metallurgy of Iron”. I: F. Oeters, R. Steffen (red.): Metallurgie . teip 2 . Verlag Stahleisen, Düsseldorf 1982, ISBN 3-514-00260-6 .
- Association of German Ironworkers (Ed.): Felles representasjon for jernbearbeidingsindustrien . 17. utgave. Verlag Stahleisen, Düsseldorf 1970.
- Fritz Toussaint: Jernens vei . 6. utgave. Verlag Stahleisen, Düsseldorf 1969.
- Otto Johannsen (på vegne av Association of German Ironworkers): Jernens historie . 3. Utgave. Verlag Stahleisen, Düsseldorf 1953.
- Robert Durrer : Grunnleggende om jernproduksjon . Verlag Francke, Bern 1947, s. 56-58 .
- Johann Christian zu Solms-Baruth, Johann Heinrich Gottlob von Justi: Avhandling av jernhamre og høyovner i Tyskland. Rüdiger, Berlin / Stettin / Leipzig 1764. (E-bok: Becker, Potsdam 2010, ISBN 978-3-941919-73-0 )
- AF Holleman , E. Wiberg , N. Wiberg : Lærebok for uorganisk kjemi . 102. utgave. Walter de Gruyter, Berlin 2007, ISBN 978-3-11-017770-1 .
- Peter Atkins : Fysisk kjemi . 2. utgave. Wiley-VCH, Weinheim 1996, ISBN 3-527-31546-2 .
weblenker
- Bilder av alle metoder for jern- og stålproduksjon og videreforedling
- Fra jernmalm til råjern: masovnen - struktur
- Radwerk IV masovnsmuseum i Vordernberg
- Jun-Ichi Kokado: Den tekniske utviklingen i den japanske stålindustrien ( Memento fra 17. januar 2008 i Internet Archive )
Individuelle bevis
- ↑ Hohofen . I: Heinrich August Pierer , Julius Löbe (Hrsg.): Universell leksikon om nåtid og fortid . 4. utgave. teip 8 . Altenburg 1859, s. 472 ( zeno.org ).
- Irts Wirtschaftsvereinigung Stahl (red.): Fakta om stålindustrien i Tyskland 2020 . ( stahl-online.de [PDF; 3.4 MB ; åpnet 15. mars 2021]).
- ↑ a b Johannsen: History of Iron , s. 9–11.
- ↑ Matthias Zwissler, Roman Landes: Undersøkelser av racingbrannprodukter , racingbrannsymposium fra IGDF International Society for Damascus Steel Research eV i Polle, 20. august 2005 ( undersøkelser av racingbrannprodukter PDF; 3,54 MB).
- ↑ Johannsen: Jernens historie , s. 11, 121.
- ↑ Johannsen: Jernens historie , s. 121-122.
- ↑ Albrecht Jockenhövel: Veien til masovnen - Tiden til middelalderens og tidlig moderne massahytter. I: Eisenland, på røttene til Nassau jernindustri. Red. Forening for Nassau antikk og historisk forskning e. V., Taunusstein 1995, ISBN 3-922027-88-1 , s. 83-98.
- ↑ a b c Durrer: Grunnleggende om jernproduksjon , s. 56–58.
- ↑ Johannsen: Jernens historie , s. 133.
- ^ Meyers Konversationslexikon - Blauofen
- ↑ Generell beskrivelse av jern- og stålindustrien , s.7.
- ^ Ludwig Beck : Bidrag til jernindustriens historie i Nassau. I: Nassau Annals. Volum 33 (1902/03), s. 212.
- ↑ Michael Gechter: Bergearkeologi i Bergisches Land. I: gv-roesrath.de. History Association Rösrath eV, åpnet 18. april 2019 .
- ↑ Aufbruch ins revier , Hoesch 1871–1961, side 34
- ↑ Aufbruch ins revier , Hoesch 1871–1961, side 43
- ↑ Johannsen: Jernens historie , s. 296.
- ↑ a b Vanlig beskrivelse av jern- og stålindustrien , s. 8–9.
- ↑ Harald Pöcher: Kriger og kamper i Japan, som skrev historie: fra begynnelsen til 1853. LIT Verlag, Münster 2009, s. 34 begrenset forhåndsvisning i Googles boksøk
- ↑ Johannsen: Jernens historie , s. 22-23.
- ↑ Johannsen: Jernens historie , s. 35.
- D Peter Dahlmann, Gerhard Endemann, Hans Jürgen Kerkhoff, Hans Bodo Lüngen: Måter å øke effektiviteten i stålindustrien , Steel Institute VDEh. Wirtschaftsvereinigung Stahl, september 2010 ( Måter å øke effektiviteten i stålindustrien PDF 1,7 MB, s. 6 ( Memento fra 17. desember 2015 i Internet Archive ))
- ↑ a b Konstruksjon av masovn 8 i Duisburg-Hamborn i ThyssenKrupp Steel AG
- ↑ Schoppa: Was der Hochöfner… , s. 52–53.
- ^ Taube: Stålproduksjon kompakt , s. 92.
- ↑ Johannsen: Jernens historie , s. 371–372.
- ↑ a b Roger Kneip: FRA STÅLINDUSTRIENS HISTORIE - Over 25 år med bjellefritt giktstopp
- ↑ Schoppa: Was der Hochöfner… , s. 55–56.
- ↑ Generell beskrivelse av jern- og stålindustrien , s. 59.
- ↑ Schoppa: Was der Hochöfner… , s. 38–39.
- ↑ Taube: Steel Production Compact , s. 62–63.
- ↑ a b Ti år med masovn Schwelgern 2 og 38 millioner tonn svinejern ( Memento fra 29. november 2011 i Internet Archive )
- ↑ ThyssenKrupp: Første ovntur avsluttet etter 21 år: Europas største masovn blir modernisert. Pressemelding 16. mai 2014.
- ↑ Vaclav Smil: Fortsatt jernalderen. Jern og stål i den moderne verden. , Butterworth-Heinemann (Elsevier), Oxford Cambridge 2016, side 90. ISBN 978-0-12-804233-5 . Utdrag , åpnet 29. september 2016.
- ^ Tre av topp 10 verdens smeltepotter som eies av Koreas POSCO. I: Arirang News. 24. august 2013, med video (0:37 min.)
- ↑ Flat stål - levering av ramme i masovn B fullført uten ulykker ( minnesmerke fra 19. september 2015 i Internet Archive )
- ↑ Generell beskrivelse av jern- og stålindustrien , s. 101.
- ↑ a b stahl-online.de - Produksjon av råjern og stål ( Memento fra 15. januar 2012 i Internet Archive ) (I følge råjern- og stålproduksjon ( Memento fra 10. februar 2011 i Internet Archive ), verdier har vært uendret siden oktober 2007 Nettsted)
- ↑ a b Vanlig beskrivelse av jern- og stålindustrien , s. 61.
- ↑ HW Gudenau, H. Kainer, G. Pitzko, M. Scheiwe: Termisk-mekanisk oppførsel av masovnens rammeforinger. I: Stål og jern. 111 (1991) 9, s. 71-81, 188.
- ↑ Schoppa: Was der Hochöfner… , s. 43–44.
- ↑ Taube: Steel Production Compact , s. 71–73.
- ↑ Taube: Stålproduksjon kompakt , s. 84–85.
- ↑ Dickmann: Utvikling av vindovnen til masovnen ... , s.1.
- ↑ Johannsen: Jernens historie , s. 325.
- ↑ Johannsen: Jernens historie , s. 327.
- ↑ Dickmann: Utvikling av vindovnen til masovnen ... , s.4.
- ↑ Dickmann: Utvikling av vindovn for masovn ... , s.6.
- ↑ Dickmann: Utvikling av vindovn for masovn ... , s.9.
- ↑ Schoppa: Was der Hochöfner ... , s.58 .
- ^ Taube: Kompakt stålproduksjon , s.47.
- ^ Taube: Kompakt stålproduksjon , s.46.
- ^ Taube: Stålproduksjon kompakt , s.59.
- ↑ a b Winzer, Reichenstein: Utvikling av masovnsteknologi , s. 80–81.
- ↑ Innovasjonsrapport: Masovn: plastpellets i stedet for koks og tungolje
- ↑ Ved å bruke gammel plast reduserer voestalpine CO 2 -utslipp i Linz med mer enn 400 000 tonn per år. (PDF 32 kB) I: voestalpine.com. voestalpine AG, 16. juni 2007, åpnet 17. juli 2019 .
- ↑ a b Ruge, Wohlfahrt: Technologie der Werkstoffe , s. 195.
- ↑ Schoppa: Was der Hochöfner ... , s.49 .
- ↑ a b Taube: Kompakt stålproduksjon , s. 152–154.
- ↑ Schoppa: Was der Hochöfner ... , s.51 .
- ↑ a b c d Schoppa: Was der Hochöfner… , s. 85–88.
- ^ Toussaint: Der Weg des Eisens , s.65 .
- ^ Grebe: Oppføringen til masovnen til Möller og Koks , s. 95-101.
- ^ Grebe: Oppvarming av masovnen til Möller og Koks , s. 101-109.
- Zer Winzer, Reichenstein: Utvikling av masovnsteknologi, s.79 .
- ^ Grebe: Oppføringen til masovnen til Möller og Koks , s. 91–92.
- ^ Grebe: Oppføringen til masovnen til Möller og Koks , s. 104-107.
- Kins Atkins: Physical Chemistry , s. 1108.
- ^ AF Holleman , E. Wiberg , N. Wiberg : Lærebok for uorganisk kjemi . 102. utgave. Walter de Gruyter, Berlin 2007, ISBN 978-3-11-017770-1 , s. 897.
- ↑ a b c Taube: Kompakt stålproduksjon , s. 131.
- ↑ Schoppa: Was der Hochöfner… , s. 64–66.
- ↑ Taube: Steel Production Compact , s. 118–124.
- ↑ Schoppa: Was der Hochöfner ... , s. 88.
- ^ Taube: Stålproduksjon kompakt , s. 147.
- ↑ Schoppa: Was der Hochöfner… , s. 89–90.
- ↑ Taube: Steel Production Compact , s. 146–147.
- ↑ Schoppa: Was der Hochöfner ... , s. 90.
- ^ Taube: Kompakt stålproduksjon , s. 148.
- ↑ ThyssenKrupp: Den femte ovnen kan begynne: Stor masovn 1 i Duisburg-Schwelgen blåses igjen i begynnelsen av april etter modernisering ; Pressemelding fra 19. mars 2008, 11:00
- ↑ a b Vanlig beskrivelse av jern- og stålindustrien , s. 78–79.
- ↑ a b Taube: Kompakt stålproduksjon , s. 158–159.
- ↑ Generell beskrivelse av jern- og stålindustrien , s. 83–84.
- ^ A b Karl-Heinz Schmidt, Ingo Romey, Fritz Mensch: Kull, petroleum, naturgass: kjemi og teknologi. Vogel Verlag, Würzburg 1981, ISBN 3-8023-0684-8 .
- ^ Taube: Stålproduksjon kompakt , s. 159.
- ↑ Schoppa: Was der Hochöfner ... , s.102 .
- ↑ Generell beskrivelse av jern- og stålindustrien , s.96.
- ↑ Schoppa: Was der Hochöfner ... , s.63 .
- ↑ Bergbau-Lexikon der steinkohle-portal.de - masovn ( Memento fra 30. mars 2012 i Internet Archive )
- ↑ Om emnet klimabeskyttelse på stahl-online.de: Stål er uunnværlig for en verden med lav utslipp.
- ↑ verden Steel Association: Verden Steel i figurene 2019 . (PDF 1.9 MB) 6. juni 2019, s. 6 , åpnet 17. juli 2019 .